14 Case Studies Demonstrating the Impact of CAD in Mechanical Engineering Innovation
- Bhargava Krishna Marripati
- Feb 16, 2024
- 10 min read
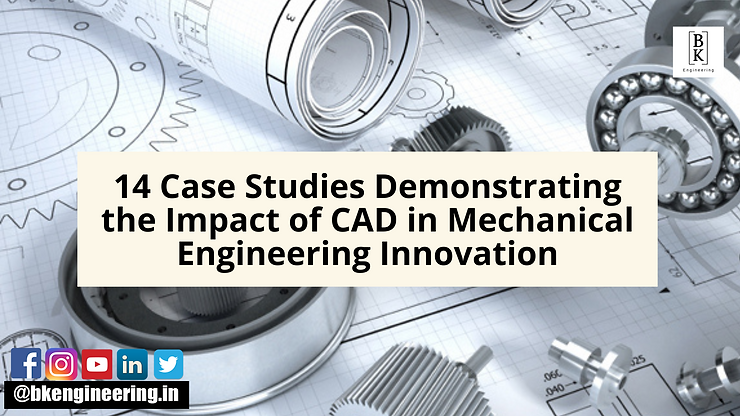
Introduction
Computer-aided design (CAD) software has revolutionized the field of mechanical engineering and paved the way for major advances in product design and manufacturing. At its core, CAD refers to the use of computer systems to assist in the creation, modification, analysis, and optimization of engineering designs. While the concept of CAD has existed since the 1960s, the technology really took off in the 1980s with the rise of personal computers and dedicated workstations.
Today, CAD is ubiquitous across every subfield of mechanical engineering, including machine design, mechatronics, thermodynamics, and more. Modern CAD software provides engineers with specialized toolsets that allow them to develop 3D models of parts and assemblies, simulate motion and forces, analyze physical properties like stress and deflection, render photorealistic visuals, and output drawings and other technical documentation.
CAD enables engineers to rapidly iterate through design cycles by making changes to 3D models or 2D drawings, rather than having to manually redraw plans. This simplifies what would otherwise be a tedious process and gives engineers more time to innovate and optimize their designs. The insights provided by CAD analysis tools also allow for more informed design decisions earlier in the development process. This results in higher quality products that perform as intended when manufactured.
In summary, CAD empowers mechanical engineers to dream up and develop next-generation products with an ease and efficiency that was unimaginable just 50 years ago. As computing power continues to improve, CAD promises to deliver even more design, analysis, collaboration, and automation capabilities that will further augment the work of mechanical engineers.
Improved Design & Prototyping
The introduction of CAD tools in the 1980s enabled engineers to efficiently create prototypes and iterate on their mechanical designs. Prior to CAD, mechanical engineers relied on manual technical drawings and drafting techniques to visualize their ideas. These processes were slow and iterative design required a significant investment of time and hand re-drafting.
CAD allowed designers to rapidly model parts and assemblies digitally, test how components fit together and evaluate designs in a virtual environment. This greatly accelerated the prototyping process as multiple concepts could be tested and refined without having to make physical models at every iteration.
With CAD, engineers could make design changes by simply modifying the digital model rather than re-drawing plans from scratch. This faster iteration enabled more innovative and optimized designs through easy experimentation with different concepts, shapes, assemblies and materials. By streamlining prototyping and making it far cheaper and easier, CAD empowered designers to push the boundaries of mechanical engineering.
The ability to quickly generate 3D CAD models, render photorealistic visuals and simulate motion also enabled better communication of complex designs with stakeholders. This allowed valuable feedback to be incorporated earlier in the design process, reducing costly errors and modifications down the track. In summary, the introduction of CAD tools marked a pivotal point where digital prototyping began supplementing and enhancing traditional physical prototyping in the mechanical engineering workflow.
Increased Productivity
CAD has significantly increased productivity for mechanical engineers and designers by automating repetitive and time-consuming tasks. In the past, engineers had to manually redraw designs from scratch if any changes were required. This was an extremely tedious process. With CAD, engineers can simply modify the existing 3D model or 2D drawings, saving huge amounts of time and effort.
CAD also enables much faster design iteration by allowing different concepts and layouts to be quickly generated, analyzed and modified. Things like changing dimensions, materials, or assembly configurations can all be done with just a few clicks. The software handles the underlying calculations and updates the models and drawings automatically. This rapid iteration allows engineers to evaluate more design options in shorter timeframes.
Powerful automation features like parametric modeling and generative design further boost productivity. Parametric modeling enables engineers to define relationships and rules between model elements. Changing one parameter then automatically propagates changes across the entire model. Generative design uses algorithms to iterate through designs and identify optimal solutions based on specified parameters and constraints. This allows high-performing design alternatives to be generated with minimal manual input.
By significantly reducing the time spent on repetitive drafting and design tasks, CAD enables engineers to focus their efforts on higher value aspects like innovation, analysis and project management. More iterations and design changes can be evaluated in compressed timeframes. CAD's automation and flexibility have been instrumental in boosting design productivity.
Enhanced Accuracy
CAD software has enabled mechanical engineers to achieve much higher levels of precision and accuracy in their designs, reducing human errors that previously led to flawed products. By creating digital 3D models and running extensive simulation and analysis, CAD tools identify problems while the product is still in the virtual design phase.
Engineers can test parts to the smallest possible tolerances and simulate real-world stresses and strains on components. This catches issues with improper fit, incorrect material selection, performance failures under load, and more. CAD allows infinitely tweaking a design to optimize it, something not possible with hand drawings and physical prototypes alone.
The immediate feedback provided by clash detection, motion simulation, and advanced rendering gives engineers confidence they have found the optimal balance of form and function. Parts designed in CAD can be manufactured to incredibly tight tolerancies thanks to the precision of CNC machines controlled by CAD files.
By minimizing human error and enabling micron-level precision, CAD has improved the performance, reliability, and longevity of mechanical products. Flaws are identified and eliminated before a physical prototype is ever built. This boosts quality while saving enormous amounts of money previously spent on physical reworking and remanufacturing.
Overall, the accuracy gains from CAD have been instrumental in mechanical engineering's ability to create highly complex products and push the boundaries of innovation. Without CAD, many of today's advanced mechanical designs would simply not be possible.
Advanced Simulation
CAD allows engineers to digitally simulate and analyze designs to a degree not previously possible. Tools like finite element analysis (FEA) and computational fluid dynamics (CFD) enable advanced simulation right from the design stage.
FEA breaks down a CAD model into tiny elements and calculates how each element deforms under different types of stresses and forces. This reveals insights on structural integrity, safety factors, fatigue life, deformations, and more. FEA allows rapid virtual testing of designs rather than time consuming physical prototyping and testing. Engineers can optimize parameters and iteratively refine the design based on simulation results.
CFD is used to simulate fluid flow, heat and mass transfer, chemical reactions, and other fluid behavior. This helps evaluate aspects like aerodynamics, cooling, fluid forces, and component interactions for complex products with fluids. CAD-based CFD provides visualizations and quantifiable data on flow fields, velocities, pressures, and temperatures across the 3D model.
These advanced simulations give crucial feedback to engineers on theoretical performance and behavior under real-world conditions. CAD integrates the simulation capabilities directly into the design workflow rather than requiring lengthy hand-offs to analysis teams. This facilitates data-driven design refinements and decisions to achieve optimal performance, safety, and durability.
By enabling rapid what-if analysis with simulation, CAD allows engineers to thoroughly evaluate candidate designs digitally before manufacturing. This reduces reliance on costly physical prototypes and saves enormous time and money in bringing better products to market faster.
Specialized Tools
Computer-aided design (CAD) software offers a wide range of specialized tools and capabilities tailored to the unique needs of different engineering domains. This allows mechanical engineers to select the CAD system that aligns closely with their specific use cases and design requirements.
One area where specialized CAD tools have made a major impact is in sheet metal design and fabrication. While regular 3D CAD modeling software can create sheet metal parts, dedicated sheet metal CAD packages include intelligent features like flange and bend calculations, punching tool design, and flat pattern creation. This automates complex mechanical processes that were previously manual and labor-intensive.
Leading sheet metal CAD tools like SolidWorks, Autodesk Inventor, and Siemens NX allow engineers to quickly design enclosures, racks, brackets, and other sheet metal components. The software automatically generates material cut lists, bending sequences, and manufacturing plans to streamline fabrication. Constraints help avoid costly design errors. Studies show sheet metal design efficiency improves by over 60% with specialized CAD versus manual methods.
For injection mold design, programs like Moldflow provide advanced mold filling and cooling analysis. This enables engineers to simulate and optimize the injection molding process on the computer first. Specialized CAD tools for mold design can predict potential manufacturing defects and material stresses. This reduces costly rework and physical prototyping iterations later. Intelligent mold design tools also automate repetitive design tasks like parting surfaces, ejector pins, and cooling channels to boost engineering productivity.
Collaboration & Communication
CAD software has significantly improved collaboration and communication between mechanical engineers, enabling better coordination within design teams and more effective visualization of concepts.
With CAD tools, multiple engineers can work on the same digital model and see each other's changes in real-time. This facilitates better discussion of ideas, rapid iteration, and integration of feedback from different team members. File sharing capabilities also allow mechanical engineers across locations to coordinate seamlessly on joint projects.
Powerful 3D visualization and rendering capabilities in CAD programs help engineers communicate design concepts more effectively to both technical and non-technical stakeholders. Photorealistic renderings, animations, and virtual walkthroughs created with CAD allow customers, managers, and manufacturers to understand the form and function of proposed products in an intuitive visual format.
CAD also integrates well with product data management (PDM) and product lifecycle management (PLM) systems, helping manage workflows and enabling automatic updates when changes are made to a master CAD model. This further aids coordination, ensuring everyone is working off the latest design information.
Overall, the collaboration and communication affordances provided by CAD have streamlined teamwork, problem-solving, and decision-making across the mechanical engineering process. Better coordination ultimately leads to improved product quality, reduced errors, and faster development cycles.
Manufacturing Integration
CAD software has played a pivotal role in integrating the design and manufacturing processes in mechanical engineering. The ability to transfer CAD files directly to computer numerically controlled (CNC) machining equipment has enabled a seamless transition from design to production.
Before CAD, hand-drawn technical drawings had to be interpreted and manually translated into machining instructions. This was a slow, error-prone and tedious process. CAD allows the generation of manufacturing-ready files with all the required dimensions, tolerances, surface finishes and other production specifications built right into the 3D model.
CNC machining equipment can directly ingest CAD models to automatically generate toolpaths and machining code. This reduces the time required for production preparation while minimizing human errors. Parts can move from design to finished manufacture much quicker thanks to the integration enabled by CAD systems.
Some examples of seamless manufacturing integration facilitated by CAD include:
Exporting a CAD assembly model from SolidWorks directly to a 3D printer for rapid prototyping of design concepts. This accelerates the testing and refinement process.
Generating CAM toolpaths from a CAD model in Siemens NX that are deployed directly on a 5-axis CNC mill. The mill then machines the part automatically based on the CAD specifications.
Using CAD embedded manufacturing modules like Delcam PowerMill to program multi-axis CNC mills. The CAM programming is integrated into the CAD software for efficient workflow.
Incorporating GD&T (geometric dimensioning and tolerancing) into CAD models so that the CNC equipment automatically machines parts to meet the specified tolerances.
Using PLM (product lifecycle management) software to coordinate CAD design, simulation, quality control and manufacturing in one integrated system.
Overall, the manufacturing industry has embraced CAD technology to connect design with production. This integration delivers tremendous improvements in speed, quality and efficiency across the product development lifecycle. CAD facilitates a smooth handover from design to the shopfloor, enabling rapid product realization.
Sustainability
CAD has enabled engineers to design products and systems that are much more sustainable and environmentally-friendly compared to the pre-CAD era. The ability to accurately model and simulate designs digitally has allowed engineers to optimize for sustainability in ways not possible before.
Key examples of sustainability improvements enabled by CAD include:
Material reduction - CAD allows engineers to precisely design components and systems to reduce material usage and waste. By simulating and testing digitally, excess material can be eliminated.
Energy efficiency - The ability to iteratively refine and simulate designs with CAD results in products that are highly energy efficient without compromising on performance. HVAC and renewable energy systems are prime examples.
Renewable energy - CAD tools have been instrumental in designing and commercializing products like solar PV panels, wind turbines and electric vehicles. The complex modeling needed is only possible with CAD.
Lifecycle analysis - Sustainability needs to consider the full lifecycle. CAD enables predictive modeling and simulation of lifespan, usage patterns and recyclability during the design phase itself.
Biomimicry - CAD allows engineers to closely study and simulate nature's optimized designs. These biomimetic principles are then incorporated into sustainable product and architecture design.
The unparalleled digital modeling capabilities offered by CAD equips today's engineers to develop innovative solutions to pressing sustainability challenges. As CAD tools continue to improve, engineers will have an ever-expanding palette at their disposal to transform our unsustainable practices and usher in a sustainable future.
Future Outlook
CAD software has come a long way, but many exciting innovations still lie ahead. Here are some of the key developments we can expect to shape the future of CAD:
Artificial Intelligence
AI is already transforming many aspects of mechanical engineering. In CAD, AI promises to automate repetitive design tasks, optimize workflows, and even suggest creative design alternatives that engineers may not have considered. Generative design using AI can lead to organic, lightweight shapes that are difficult for humans to conceptualize. AI can also analyze simulation data to derive engineering insights.
Virtual & Augmented Reality
By creating immersive 3D environments, VR and AR will change how engineers interact with CAD models. Engineers will be able to walk around and manipulate virtual prototypes, identifying design flaws earlier. AR overlays will guide shop floor workers during manufacturing. VR collaboration will allow globally distributed teams to jointly review CAD models.
Generative Design
Already touched upon in the context of AI, generative design is a gamechanger. Engineers specify design goals like performance criteria, weight limits, manufacturing methods etc and the software generates multiple creative options. This automated concept generation saves time and results in high-performing, organic designs.
Cloud Computing
The future is cloud. With reliable internet, the need for powerful local workstations is reducing. Cloud-based CAD allows seamless collaboration in real-time, with no limit on model size or computing power. It also enables access to computing resources like simulation and rendering on demand.
Powerful cloud servers running AI and generative algorithms will be able to churn out design variants for engineers to evaluate. The cloud also facilitates easy software updates and seamless data backup.
Overall, innovations in AI, VR, generative design and cloud computing will drive CAD to new heights, opening up novel design possibilities while increasing efficiency. The future looks bright and exciting for CAD software and mechanical engineering innovation.
Comments