9 Ways to Optimize Your CAD Models for 3D Printing in Mechanical Engineering
- Bhargava Krishna Marripati
- Feb 15, 2024
- 9 min read
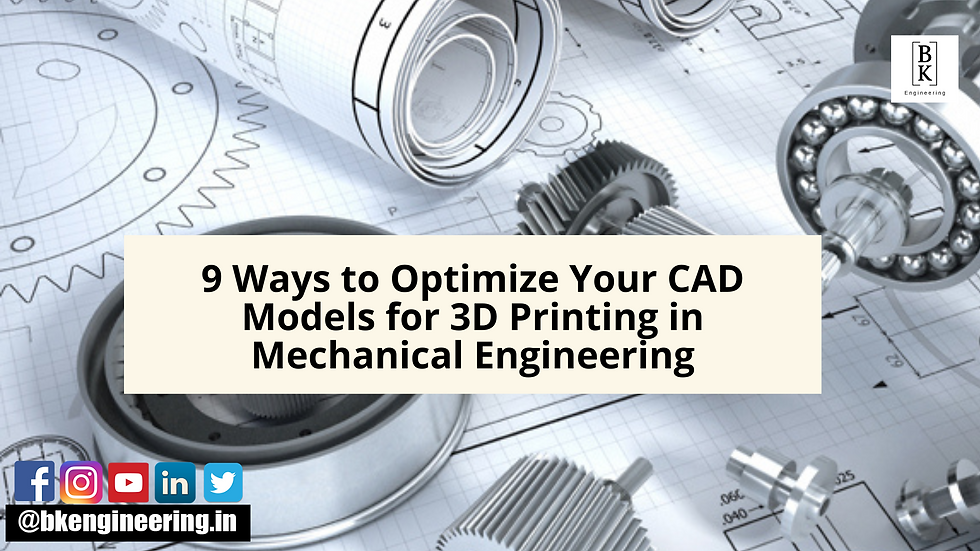
1. Simplify Geometries
When designing parts for 3D printing, start by simplifying the geometry as much as possible. Complex models with lots of intricate details can be difficult and time-consuming to print. Instead, focus on the key features the part needs to function properly.
Reduce the number of small features like holes, ribs, or text. These fussy details are difficult for the printer to recreate accurately and can lead to print failures. Stick to the essentials needed for the part to work.
Use basic geometric shapes like squares, rectangles and cylinders rather than complex freeform curves and surfaces. Printers find it easier to smoothly fill in layers for fundamental shapes.
Avoid adding any tiny precision features smaller than around 0.4mm. Most desktop 3D printers cannot print details below this threshold, resulting in rough or inaccurate surfaces.
By removing unnecessary elements and optimizing your CAD model geometry early on, you can dramatically reduce print time and chances of print failure. Printers will have an easier time recreating the simplified part layer by layer.
2. Design Parts as Assemblies
When 3D printing complex mechanical parts, it is often better to split the design into sub-assemblies that can be printed separately and then joined together. This allows you to optimize the orientation and print settings for each component. It also avoids common printing issues caused by large, intricate models.
Design your assemblies in CAD software by modeling connectors between the separate components. This allows the parts to precisely fit together after printing. Some best practices include:
Split Into Sub-Assemblies - Identify sections of your model that can be divided into logical sub-assemblies. Keep components under a certain max size based on your printer build volume.
Design Proper Connectors - Add connectors like pins, joints, and fasteners so the sub-assemblies can be mechanically assembled after printing. Design connectors that interlock cleanly without needing supports.
Account for Tolerances - Allow for print tolerance of around 0.1-0.3mm when modeling connectors and assembly clearances. 3D printing is not always dimensionally accurate, so design assemblies with appropriate tolerances.
By designing your complex mechanical parts as assemblies, you can optimize the orientation and print settings for each component. This will result in higher quality 3D printed parts that assemble properly.
3. Optimize Wall Thicknesses
When designing parts for 3D printing, one of the most important considerations is setting the optimal wall thickness. The wall thickness will impact the part's strength, material usage, print time and quality.
Follow your printer manufacturer's guidelines for minimum wall thickness based on the nozzle size. Most FDM printers require walls to be at least 2-3x the nozzle diameter. For SLA printers, the minimum is around 0.7-1mm. Going below these thresholds risks print failures and quality issues.
Account for the strength characteristics and printing behavior of your chosen material. For example, flexible materials can be printed thinner than rigid plastics. Parts under high stress need thicker walls for sufficient strength. Reference material datasheets for recommendations.
Balance strength requirements with print time. Thinner walls print faster but compromise durability. Medium thicknesses around 2mm provide a good balance. Critical load-bearing features may need 4-5mm. Solid blocks maximally strengthen parts but require very long print times.
For complex organic shapes, variable thickness walls that follow form can save material and weight while maintaining strength. Use thicker fortifications only where needed.
Whenever possible, orient the part to minimize thin cross-sectional walls, which are more prone to breakage.
By optimizing your model's wall thicknesses for the printer, materials, and application, you can achieve faster print times while still guaranteeing the required structural integrity. Print tests will help dial in the ideal values.
4. Orient Parts Properly
One of the most important aspects of optimizing mechanical CAD models for 3D printing is properly orienting the part on the print bed. The orientation can have significant effects on print time, material use, and part strength.
When orienting parts, the goal should be to minimize overhangs and reduce the need for support structures. Overhangs are sections of the print where layers have nothing underneath them. This commonly happens when printing angles greater than 45 degrees. In these situations, supports are required during printing to prevent drooping or collapse. Supports add print time, use extra material, and can be tricky to remove.
To avoid overhangs, orient the part so the majority of surfaces are printed flat against the build plate or only have shallow angles. Some things to consider:
Place high-detail surfaces face down. This takes advantage of the highest resolution on the first layers.
Rotate the part so the shortest dimension is on the Z axis. This minimizes layer height and reduces print time.
Orient parts vertically for columns or cylinders to avoid printing overhangs around the circumference.
Proper orientation also optimizes part strength based on the expected load direction. For example, parts will be strongest when layers are perpendicular to the primary force. Consider analysis like FEA to determine the optimal orientation.
Lastly, orientation affects cooling. Parts should be oriented to allow even cooling of layers. Avoid situations where one section cools quickly while another overhang section is still being printed. The uneven cooling can cause warping or delamination.
Taking the time to thoughtfully orient your CAD parts will pay off with faster prints, less material use, and optimal mechanical properties. Analysing overhangs, supports, strength, and cooling will lead to a smarter orientation.
5. Design Efficient Supports
One of the keys to optimizing mechanical CAD models for 3D printing is designing efficient support structures. Support structures are crucial for successfully printing overhangs and complex geometries. However, supports also increase print time, material use, and post-processing work.
When designing supports, follow these best practices:
Adhere to Overhang Rules: Most slicers use a 45 degree rule - any overhangs greater than 45 degrees will require supports. Some flexible materials allow for more overhang before needing supports. Analyze overhangs and only use supports where truly needed.
Use Optimized Support Patterns: Choose an optimal support pattern based on your part's geometry. Dense supports or a lattice pattern works well for large overhangs. Tree supports help reduce material use and removal time.
Position Supports for Easy Removal: Situate supports so they can be easily removed after printing. Avoid overhanging supports as much as possible. Place supports uniformly to minimize risks of part warping.
Efficient support design takes some trial and error. But following these tips will help mechanical engineers 3D print complex parts faster, with less material waste and post-processing work. Analyze overhangs, utilize optimized patterns, and position for easy support removal.
6. Choose Suitable Infill
Infill refers to the structure inside the walls of a 3D printed object. It's usually a lattice or grid pattern that provides internal support.
Choosing the right infill settings can have a major impact on both the strength and print time of your parts. The key is finding the ideal balance between these two factors based on your specific mechanical design needs.
When optimizing infill, start by considering the load conditions your part will experience. Parts that need to withstand high stresses or forces will require a higher infill percentage, such as 40-60%. This adds strength but also increases print times.
For parts that don't experience high loads, a lower infill around 20% is often suitable. This greatly reduces print time while still providing adequate strength for the application.
You can also adapt the infill pattern or type to suit the design. For example, gyroid and cubic infills offer a good compromise between print speed and strength. Linear patterns print fastest but can compromise strength on the horizontal plane.
Finally, consider how you orient the infill structure. Aligning it with the forces applied to your part can maximize strength along those load paths. Rotating the infill 45° or 90° from the main axes may provide benefits depending on the design.
Experiment with different infill settings when optimizing your CAD models. Pay attention to how infill orientation, pattern, and density impact the print time versus strength trade-off. Finding the right balance will allow you to 3D print functional mechanical parts faster.
7. Refine Problematic Areas
When 3D printing mechanical parts, certain geometries can cause issues during the printing process. Areas like sharp corners and thin regions tend to have lower strength and may warp or deform. Optimizing these areas before printing can improve part quality.
One technique is to add fillets and radii to sharp corners. The smoother curvature distributes stresses over a larger volume and reduces the likelihood of cracking. For functional parts, balance larger fillets for strength with smaller ones for fit and clearance.
Trapped powder inside hollow sections can also lead to defects. Adding small escape holes allows powder removal before and after printing. Position the holes strategically to minimize visible surfaces.
Thin regions like ribs and bosses can droop or fail in the middle layers. Adding a rib structure reinforces thin features while minimizing material use. Orient ribs vertically for better strength than horizontal ribs. Focus on ribbing walls, bosses, pads, and any thin or undersupported areas.
Taking the time to refine tricky geometries before printing can prevent wasted time and material. Simple changes like fillets, escape holes, and ribs make parts more robust and optimized for 3D printing. Evaluate your model and address weak points proactively.
8. Perform Design Validation
Before sending your CAD model to print, it's critical to validate the design by previewing it in your slicer software and test printing iteratively. This helps catch any potential issues that could ruin a print or waste time and materials.
When previewing the layer view in your slicer software, look for the following:
Overhangs - Any areas without support can droop or sag if the angle is too sharp. Add supports in these areas.
Bridges - Sections that span a gap without underlying support. Ensure bridged areas are not too long.
Thin walls - Very thin vertical or horizontal walls may not print properly. Consider making them thicker.
Clearance - Check that moving parts have enough clearance to move freely after printing.
Test print your model and inspect carefully:
Monitor the first layers to ensure good adhesion and confirm your raft, brim or skirt is working properly.
Check for signs of sagging, warping or layer shifting and adjust if needed.
Iterate by tweaking printer settings, orientation, infill, supports and model design issues.
Validate your model fully before committing to a final print. Good design validation prevents wasted time and materials.
9. Optimize Printer Settings
Getting the most efficient and high-quality 3D prints starts with optimizing your printer settings. Here are some best practices:
Calibrate Your Machine
Before printing anything, it's crucial to fully calibrate your 3D printer. Calibration ensures components are aligned, leveled, and operating smoothly. Go through your printer's full calibration sequence, checking the guide rods, belts, hotend, and print bed. For the best dimensional accuracy, precisely calibrate the steps/mm on each axis.
Use Quality Filament
Not all filaments are made equal. Quality filament from reputable suppliers is recommended for mechanical parts. The diameter tolerance and consistency of the filament matters, as inconsistencies can lead to clogged nozzles or weak prints. Opt for filaments optimized for mechanical applications.
Dial In Print Settings
Take the time to properly dial in all your print settings, including temperature, print speeds, retraction, and cooling. Most slicers provide presets, but fine tuning for your specific printer and part will produce better results. Run test prints to optimize settings like temperature, print speed, layer height, infill, etc.
Monitor the First Layers
The first few layers set the foundation for the entire print. Closely monitor the first layers; if they don't adhere well or gaps appear, stop the print and re-level the bed. Adjust the z-offset and try again until you achieve a solid first layer.
Choose the Right Nozzle
Larger nozzles and layer heights speed up prints significantly but reduce detail and precision. For mechanical parts, a smaller nozzle like 0.2 or 0.4mm is recommended for precise details, tolerances, and a good surface finish. Only go larger if timeline is critical but precision is not.
By properly calibrating your machine, using quality filament, optimizing print settings, monitoring initial layers, and selecting the ideal nozzle size, you'll achieve faster, higher-quality 3D prints. Dialed-in printer settings let your optimized mechanical CAD models shine.
10. Post-Process Parts
Post-processing involves additional steps taken after a part is 3D printed to improve the final product. Properly post-processing parts can enhance the quality, appearance, and tolerances of 3D printed mechanical components.
Common post-processing techniques for 3D printed parts include:
Remove Supports
Support structures help hold up overhanging sections while printing, but need to be detached after the print is finished. Support material can often be removed by hand, using pliers or flush cutters to clip away supports. For difficult to reach areas, an Exacto knife or rotary tool can help slice away excess material. Be sure to remove all remnants of support material so the final surface is smooth.
Sand/Finish Surfaces
The layer-by-layer printing process can leave visible striations and a rough texture on the exterior walls of a part. Sanding helps smooth down the stepped layers into a more uniform surface. Start with a coarse grit sandpaper (100-150) to rapidly remove bigger imperfections, then gradually step down to finer grits (up to 2000) for polishing. Alternative finishing techniques include bead blasting or vapor smoothing.
Improve Tolerances/Cosmetics
Post-processing can also improve the dimensional accuracy of printed parts. Sanding, machining, or tumbling can help bring critical mating surfaces and holes to more precise tolerances. Techniques like priming, painting, and plating can also give parts a more refined, finished look and feel.
Properly leveraging post-processing techniques helps 3D printed mechanical parts meet functional requirements while achieving a smooth, polished appearance. Parts can be sanded, machined, coated, and finished to improve quality and cosmetics after initial printing.
Comments