Introduction to Plastic Mold Design
- Bhargava Krishna Marripati
- Feb 7, 2024
- 5 min read
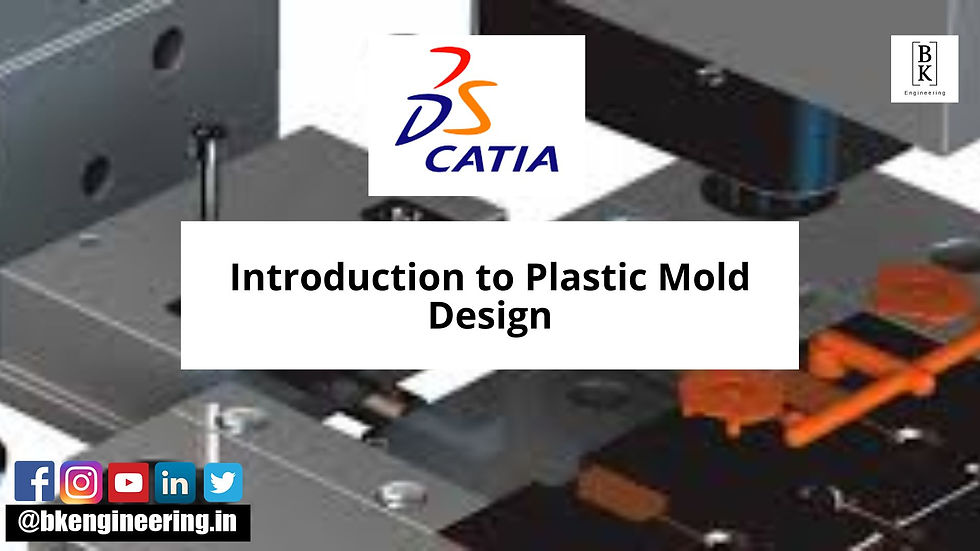
Introduction to Plastic Mold Design
Injection molding is a manufacturing technique for producing plastic parts in high volume. It works by injecting molten plastic material into a mold cavity, where it cools and hardens into the final part. Some of the major advantages of injection molding are high production rates, consistency, and low labor costs once the initial mold design is completed.
Injection molding is used to make a huge variety of plastic parts across many industries, including automotive, medical, consumer products, and more. Typical applications include plastic housings, containers, bottle caps, mechanical parts, and toys. The most commonly injection molded plastics are:
- Polypropylene (PP) - Used for food containers, appliances, automotive parts, industrial packaging, and consumer products. Provides good chemical resistance, durability, and flexibility.
Acrylonitrile Butadiene Styrene (ABS) - Used for automotive trim components, toys, musical instruments, pipe fittings, and golf club heads. Provides high impact strength and rigidity.
Polycarbonate (PC) - Used for medical devices, eyewear lenses, bulletproof glass, CDs/DVDs, automotive lenses, and transparent building panels. Provides high strength and temperature resistance.
Nylon (PA) - Used for automotive parts, machinery components, electrical insulators, sporting goods, bearings, gears, and more. Provides high strength, durability, and corrosion resistance.
The primary equipment needed for injection molding includes an injection molding machine, a mold with core and cavity components, and a plastic feed system (hopper, auger, nozzle). Controls for heating, cooling, pressure, and cycle timing are also critical. The mold is often made from tool steel or aluminum alloy and custom machined for each part design. Proper mold design is essential for successful injection molding with high-quality results.
The Injection Molding Process Explained
Injection molding is a manufacturing process for producing plastic parts. There are four main stages in the injection molding process:
Clamping
The clamping unit of the injection molding machine holds the mold closed during the injection process. Typically, a hydraulically powered ram pushes the mold halves together with great force to prevent the mold from opening during the injection of the molten plastic. The amount of clamping force required depends on the size of the part being produced.
Injection
During the injection stage, the raw plastic material is melted in the injection unit and forced into the mold cavity through a sprue, runner, and gate system. The molten plastic enters the mold through a nozzle pressed tightly against the sprue bushing. Pressure is applied for the duration of the injection process to pack the mold. This packing pressure is maintained until the gate solidifies.
Cooling
Once the gate has solidified, the packing pressure is released. The molten plastic in the mold cools until it has solidified sufficiently for the part to be ejected from the mold. The cooling time is dependent on the wall thickness and number of cavities in the mold. Cooling is often assisted by circulating coolant through channels in the mold. Proper cooling is critical to achieving the proper crystallization in semi-crystalline plastics.
Ejection
After the predetermined cooling time has passed, the clamping force is released and the mold separates. As the mold opens, ejector pins push the part out of the mold. The mold then closes again and the clamping force is reapplied, allowing the next injection molding cycle to occur.
The injection molding cycle consists of the above four stages and is repeated continuously with a frequency ranging from a few seconds to a few minutes depending on the machine and mold size.
There are several different types of injection molding processes, including:
Thermoplastic injection molding - Uses thermoplastic resins like polyethylene, polypropylene, polystyrene, and other commodity resins.
Thermoset injection molding - Uses thermoset resins like polyurethane, epoxy, and unsaturated polyester. The part cannot be remelted and recycled after molding.
Gas-assisted injection molding - Uses an inert gas like nitrogen to create hollow sections in the part, reducing material usage and cooling times.
Multicomponent molding - Uses two or more materials injected from different barrels allowing overmolding in one process.
The right injection molding process must be selected to match the material being used.
Designing Parts for Injection Molding
Designing parts specifically for injection molding is critical to creating high-quality, cost-efficient molds. There are several key design principles to keep in mind:
Parting Lines
The parting line is the plane in the part design where the two mold halves separate. Parts should be designed so that the parting line is along a relatively flat, uniform surface. Avoid parting lines that cut across holes, ribs, bosses, or other complex geometries. The parting line influences the location of gates, ejectors, and overall mold construction.
Draft Angles
Draft angles are added to vertical surfaces in the part design to assist in demolding. Angles between 1-3 degrees typically work well. Without draft angles, parts can get stuck in the mold. Outside vertical walls need a draft added, while inside vertical walls may need a reverse draft removed.
Uniform Wall Thickness
Keep wall thickness uniform throughout the part design. Changes in wall thickness can lead to uneven cooling, sink marks, and warpages. Recommended thickness depends on the material, but keep walls between 0.8-2.5mm. Thicker walls increase material use and cycle times.
Ribs and Gussets
Adding ribs and gussets is an effective way to strengthen parts without increasing overall wall thickness. Place ribs at natural stress points and flow them with the contours of the part. Make ribs thick enough to maintain strength but thin enough to fill and pack out.
Radii
Sharp corners act as stress concentrators and should be avoided. Add generous radii to corners and fillets to neighboring walls. This helps avoid crack propagation. Radii should be at least 10% of the wall thickness. Larger radii improve mold flow and part strength.
Common Mold Features
A well-designed injection mold contains many common features that enable the mold to function properly and efficiently produce quality parts. Three key components of any injection mold are the gate, ejector system, and vents/overflows.
Gates
The gate is the opening through which molten plastic enters the mold cavity. Several types of gates may be used:
Sprue gates - A simple gate directly connecting the sprue (the channel from the nozzle) to the part cavity. This is the most common and cost-effective gate type.
Pin gates - A restricted gate formed by a pin in the mold. This creates a weak point where the gate easily breaks off the part after molding.
Film gates - A tiny, thin gate section that shears off and leaves no vestige on the part.
Fan gates - A gate with multiple smaller openings flowing into the part cavity. This promotes even filling.
The gate must be positioned so that the cavity fills evenly and completely before the plastic freezes off. Gates are typically located on thicker sections or along parting lines. Multiple gates may be required for larger parts.
Ejection Systems
Ejector systems remove parts from the mold after molding. This usually consists of ejector pins that push the parts off of the mold core when the mold opens.
The pins should be located on flat surfaces of the part geometry. There must be enough ejector pins to uniformly eject the part without distortion.
Vents and Overflows
As the mold cavity fills with molten plastic, air, and gases must be vented out to avoid defects from trapped bubbles.
Output trimmed for rendering. Click copy for full output.
1. The Plastic Whisperer's Guide to Injection Mold Mastery
2. Unlocking the Secrets of Flawless Plastic Mold Design
3. Plastic Mold Design Demystified: The Beginner's Blueprint for Molding Perfection
Learn plastic mold design: part design, defect fixes, materials, thickness, undercuts, supplier collaboration for quality, and cost-effective molds.
Opmerkingen