Types of Industrial Conveyors: Uses & Applications in Manufacturing
- Bhargava Krishna Marripati
- Feb 26
- 17 min read
Updated: 9 hours ago
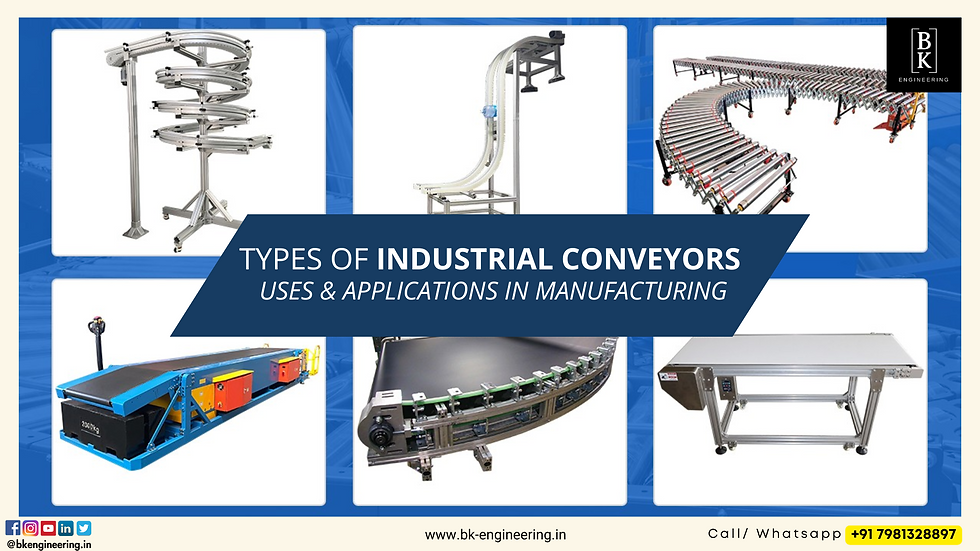
Table of content:
Introduction to Conveyor Systems
A conveyor system is a mechanical equipment that efficiently moves materials from one location to another. Conveyors are particularly useful for transporting heavy or bulky materials. They are crucial in industries for facilitating material and product flow during manufacturing, warehousing, and distribution, offering benefits like increased efficiency, reduced labor costs, improved safety, and enhanced productivity. Various types of conveyors, such as belt, roller, overhead, screw, and pneumatic conveyors, cater to specific applications and material handling needs. Understanding these types is essential for selecting the right system for a given application. In this blog, we'll explore the different types of conveyor systems, their mechanisms, applications, and cost and maintenance factors, with insights.
Gravity Conveyors

Gravity conveyors are a fundamental component in the world of material handling and logistics. They provide a cost-effective, efficient way to move products from one point to another without the need for external power sources.
These conveyors rely on gravity or manual force to move items, making them a sustainable and low-maintenance option for many industries. This blog will walk you through what gravity conveyors are, their types, benefits, applications, key features, and more.
Types of Gravity Conveyors

Gravity Roller Conveyors
Application: Suitable for handling heavier loads like boxes, totes, and pallets. Frequently used in loading docks, assembly lines, and packaging stations.
Industries: Warehousing, manufacturing, retail distribution, automotive, and e-commerce.
Mechanism: Operates using rollers mounted on a frame, allowing materials to move via gravity or manual force. The rollers can be spaced according to the load size to prevent sagging or tipping.
Cost & Maintenance: Low cost; requires occasional lubrication of rollers and inspection of frame integrity. Replacement rollers are inexpensive and easy to swap.
Key Features: Available in various roller diameters and materials (steel, plastic); can be used for both straight and curved sections. Rollers with different surface finishes are available for handling delicate or high-friction materials.
Example: In a distribution center, gravity roller conveyors move heavy cartons from sorting areas to packaging stations, streamlining the order fulfillment process.
Gravity Wheel Conveyors

Application: Ideal for lighter loads and curved paths, including irregularly shaped items. Used for fast-moving pick-and-pack lines.
Industries: Retail, packaging, warehousing, and distribution centers.
Mechanism: Uses skate wheels instead of rollers to facilitate smoother and faster movement. The multiple contact points provide better handling for smaller packages.
Cost & Maintenance: Cost-effective; minimal maintenance needed — regular checks for wheel wear and frame alignment.
Key Features: Easier to reconfigure for different layouts; better flow control for light products. Great for zigzag or curved conveyor paths.
Example: A retail warehouse may use wheel conveyors to quickly move shoe boxes through an order sorting area, allowing for seamless direction changes without slowing down the process.
Chute Conveyors

Application: Used for moving items from higher to lower points — ideal for sorting and packaging lines. Suitable for fragile goods with customized chutes.
Industries: Warehousing, food and beverage, logistics, and postal services.
Mechanism: Utilizes an inclined surface, allowing gravity to slide products downward. Speed can be controlled by adjusting the angle of the chute.
Cost & Maintenance: Low cost; requires cleaning and occasional wear checks. Materials like stainless steel or lined chutes can prevent product damage.
Key Features: Can be made from metal or plastic; customizable chute angles for better flow control. Anti-static linings are available for electronic goods.
Example: In postal facilities, chute conveyors guide parcels from sorting machines to designated bins below, minimizing manual handling.
Ball Transfer Conveyors

Application: Suitable for omnidirectional movement of flat-bottomed items — ideal for assembly lines. Used in areas where items need repositioning.
Industries: Manufacturing, automotive, and electronics.
Mechanism: Consists of mounted ball casters that enable products to move in any direction. This allows for easy rotation and alignment of heavy or awkwardly shaped goods.
Cost & Maintenance: Moderate cost; regular cleaning to prevent debris build-up in ball casters.
Key Features: Allows for easy positioning and rotation of products; perfect for workstations. Stainless steel balls for high-precision applications.
Example: Automotive assembly lines use ball transfer conveyors to maneuver car parts into the correct orientation before final installation.
Flex Conveyors
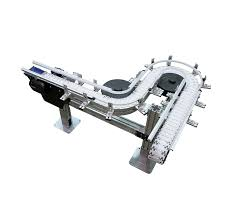
Application: Ideal for loading/unloading trucks and adapting to varying workflows. Common in e-commerce fulfillment centers.
Industries: Logistics, distribution centers, and e-commerce.
Mechanism: Extendable and flexible conveyor sections that bend into various shapes. Adjusts to fit loading dock spaces and fluctuating workloads.
Cost & Maintenance: Moderate cost; requires checks for wheel condition and frame stability.
Key Features: Highly portable; available with either rollers or skate wheels; adjustable lengths. Locking mechanisms to secure the conveyor's position.
Example: An e-commerce warehouse uses flex conveyors to load packages from sorting areas directly into delivery trucks, reducing manual carrying time.
Benefits of Using Gravity Conveyors
Cost-Effective: No electricity or motors are required, reducing energy costs.
Low Maintenance: Fewer moving parts mean minimal wear and tear.
Simple to Install and Use: Easy to set up and adaptable to different facility layouts.
Scalable: Can be extended or modified as business needs grow.
Eco-Friendly: Operates without power, contributing to sustainable practices.
Increased Efficiency: Reduces manual handling and speeds up material flow.
Versatility: Compatible with various industries and load types.
Conclusion on Gravity Conveyors
Gravity conveyors offer a simple yet highly effective way to move goods efficiently. Whether you're running a warehouse, a production line, or a distribution center, these conveyors can significantly enhance operational flow without the added cost of powered systems.
From roller conveyors that handle bulkier items to flexible conveyors ideal for dynamic workflows, gravity conveyors provide tailored solutions for diverse needs. If you're looking to integrate gravity conveyors into your business, feel free to reach out to us for expert guidance and customized systems that suit your operations!
Belt Conveyors

Conveyor systems are the backbone of modern material handling, streamlining operations and boosting efficiency across industries.
From manufacturing to logistics, these systems automate the movement of goods, reducing manual effort and enhancing productivity.
Belt conveyors are one of the most commonly used types of conveyor systems, known for their versatility and ability to transport a wide range of materials over long distances. They consist of a continuous loop of a flat, reinforced rubber or plastic belt that rotates around two or more pulleys.
The main components of a belt conveyor include:
Belt: The belt itself, typically made of rubber, PVC, or other durable materials, designed to handle the weight and abrasiveness of the conveyed materials.
Pulleys: Cylindrical drums that support and guide the belt, with one pulley acting as the drive pulley powered by a motor.
Idlers: Roller assemblies that support the belt's carrying run and return run, preventing sagging and reducing friction.
Drive unit: The motor and gearbox that provide the power to rotate the drive pulley and move the belt.
Frame: The structural support system that holds the pulleys, idlers, and other components in place.
Belt conveyors are widely used in various industries for transporting bulk materials, such as coal, grain, sand, and gravel, as well as packaged goods and other products.
They are particularly useful for moving materials over long distances, both horizontally and at inclined angles.
When selecting a belt conveyor, factors such as material characteristics, conveyor capacity, length and layout, and environmental conditions must be carefully considered to ensure efficient and reliable operation.
Let’s dive into their various types and applications:
Flat Belt Conveyors

Application: Ideal for handling all types of packaging or loose products.
Industries: Manufacturing, distribution, packaging, warehousing, and logistics.
Mechanism: Operates with a flat belt that moves over rollers or a flat surface.
Cost & Maintenance: Moderate cost; regular inspection of belt tension, rollers, and alignment is required.
Key Features: Can transport goods horizontally or at a slight incline; customizable with grip surfaces, low-friction, or food-quality materials like rubber or PVC.
Angular/Inclined Belt Conveyors

Application: Used for transferring loads between different floors or levels.
Industries: Food processing, packaging, warehousing, distribution, agriculture, and mining.
Mechanism: Inclined design with belts and cleats to prevent rollback.
Cost & Maintenance: Slightly higher cost due to added components; requires periodic checks for cleat wear and motor efficiency.
Key Features: Suitable for incline angles above 20°; moves input materials to significant heights during sorting processes.
Cleated Belt Conveyors

Application: Ideal for conveying bulk materials at an inclined angle.
Industries: Agriculture, mining, construction, recycling, and food processing.
Mechanism: Utilizes cleats attached to the belt to secure materials.
Cost & Maintenance: Moderate to high cost; maintenance involves checking cleats for damage and ensuring smooth belt movement.
Key Features: Prevents material rollback; perfect for grains, seeds, aggregates, wood chips, and packaged goods.
Aluminum Belt Conveyors
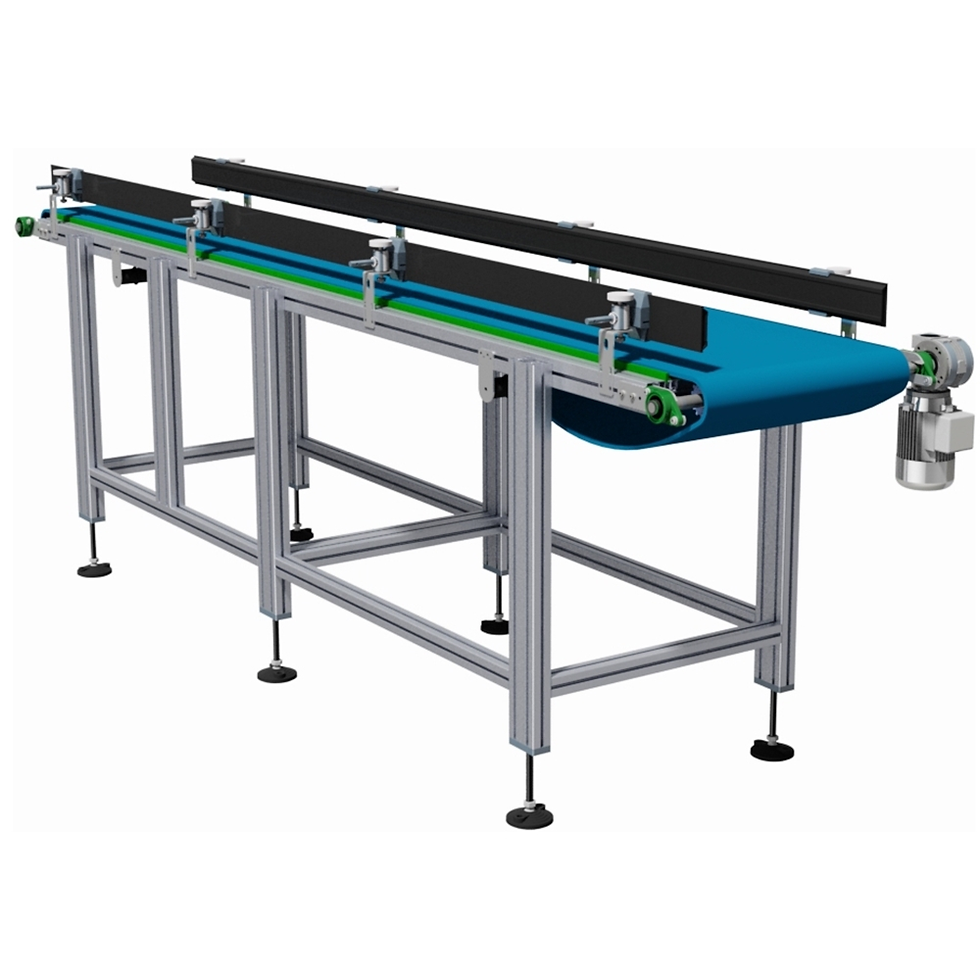
Application: Suitable for transporting goods of various shapes and sizes.
Industries: Manufacturing, packaging, automotive, electronics, and aerospace.
Mechanism: Built with lightweight aluminum frames and powered rollers.
Cost & Maintenance: Moderate cost; low maintenance due to durable aluminum structure.
Key Features: Lightweight yet sturdy; used in assembly lines and production lines.
Modular Belt Conveyors

Application: Offers flexibility for complex layouts with straight runs, curves, inclines, and declines.
Industries: Food processing, beverage production, pharmaceuticals, automotive, and logistics.
Mechanism: Composed of interlocking plastic or metal modules.
Cost & Maintenance: Moderate to high cost; easy to maintain by replacing damaged modules.
Key Features: Built with interlocking plastic or metal modules; easy maintenance and customizable configurations.
Knife Edge Belt Conveyors

Application: Designed for smooth transfer of small or delicate items.
Industries: Electronics, pharmaceuticals, packaging, and food processing.
Mechanism: Uses a thin knife edge at the end of the belt for precise item transfer.
Cost & Maintenance: Moderate cost; requires careful monitoring of belt edges to prevent wear.
Key Features: Ensures precise transfer without snagging; used for electronic components, pharmaceutical vials, and food trays.
90° Bend Belt Conveyors

Application: Change material flow direction by 90 degrees for optimized
space utilization.
Industries: Manufacturing, distribution centers, warehouses, and airports.
Mechanism: Uses bend pulleys and flexible belts.
Cost & Maintenance: Moderate cost; routine checks of bend pulleys and belt alignment are necessary.
Key Features: Efficiently handles packaged goods, boxes, cartons, and totes.
Packaging Belt Conveyors
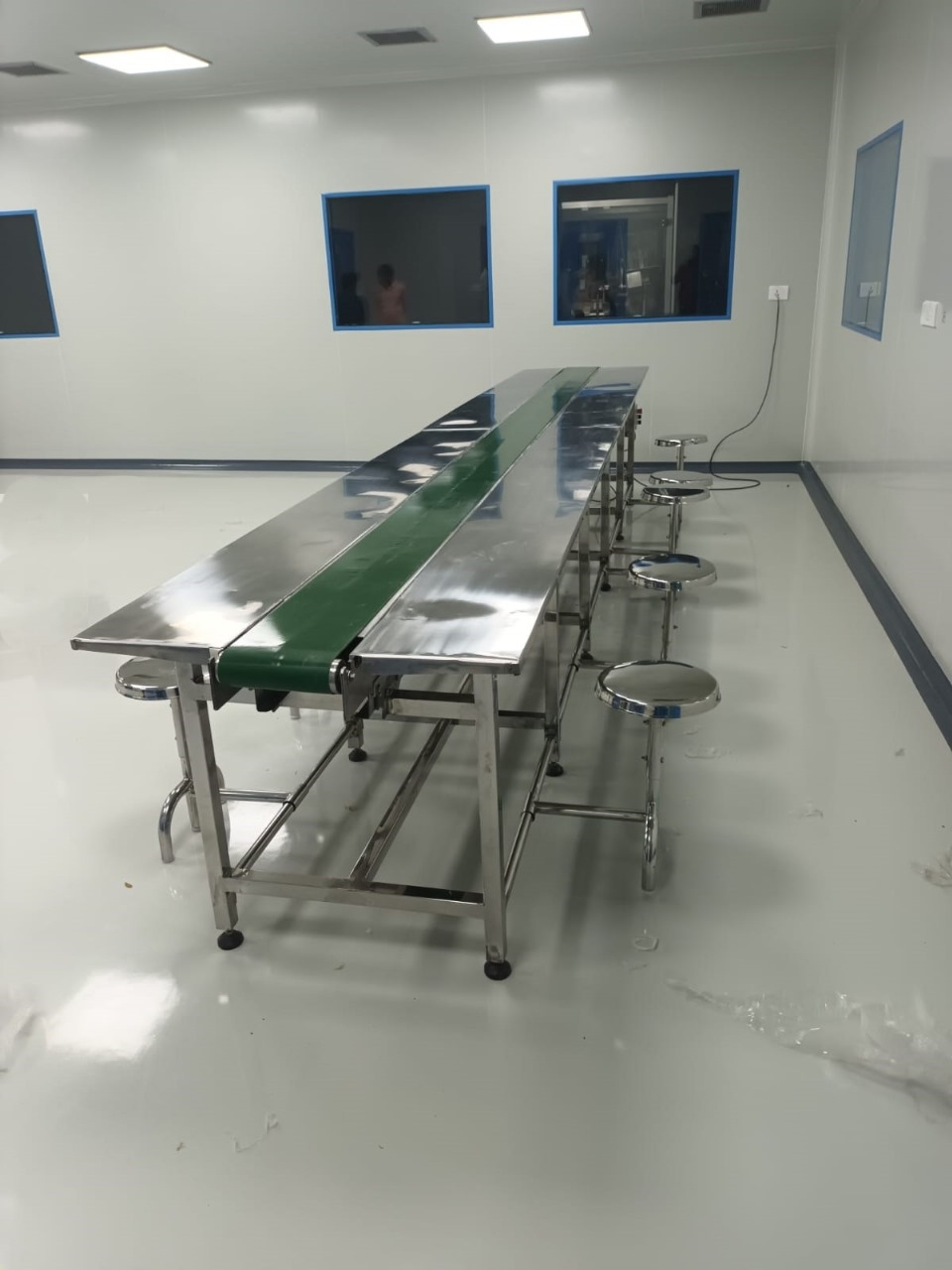
Application: Streamline packing lines by feeding products onto packaging tables.
Industries: Pharmaceuticals, cosmetics, food and beverage, and electrical tools.
Mechanism: Flat or inclined belts with adjustable speeds.
Cost & Maintenance: Moderate cost; simple to maintain with regular cleaning and lubrication.
Key Features: Automates packing processes, reduces downtime, and enhances operational efficiency.
Printer/Batch Coding Conveyors

Application: Enables batch or date coding of products in real-time along the production line.
Industries: Food and beverage, pharmaceuticals, cosmetics, and consumer goods.
Mechanism: Integrates with printing machines for on-the-go batch coding.
Cost & Maintenance: Moderate to high cost; maintenance involves cleaning print heads and ensuring belt stability.
Key Features: Ensures regulatory compliance and traceability.
Visual Inspection Belt Conveyors

Application: Facilitates quality control through integrated lighting, cameras, and sensors.
Industries: Automotive, electronics, pharmaceuticals, and food and beverage.
Mechanism: Includes sensor systems and adjustable lighting setups.
Cost & Maintenance: High cost; requires regular sensor calibration and camera cleaning.
Key Features: Detects defects, inconsistencies, or contamination in products.
Roller Conveyors
In the fast-paced world of material handling, roller conveyors have become indispensable. From warehouses to manufacturing facilities, these systems offer efficient, reliable solutions for transporting goods. Let’s dive into the various types of roller conveyors and their applications.
90 or 180 Degrees Powered Turning Rollers Conveyors

Applications:
Warehouses and distribution centers for redirecting product flow.
Manufacturing lines requiring smooth directional changes.
Logistics operations optimizing space and efficiency.
Industries:
Warehousing
Distribution
Manufacturing
Logistics
Mechanism: Utilizes motorized rollers placed at calculated angles to guide items along the curve.
Cost & Maintenance: Moderate cost with regular motor checks and lubrication.
Key Features:
Smooth directional changes without manual intervention.
Powered rollers ensure consistent movement.
Adaptable to various product sizes.
Double Deck Roller Conveyors

Applications:
Warehousing and distribution where space optimization is crucial.
Manufacturing lines handling multiple product streams.
Logistics facilities aiming for compact yet effective transport solutions.
Industries:
Warehousing
Distribution
Manufacturing
Logistics
Mechanism: Operates with synchronized rollers on both decks, driven by a shared motor system.
Cost & Maintenance: Higher cost; requires regular alignment checks and roller cleaning.
Key Features:
Dual levels optimize vertical space.
Allows parallel processing of products.
Can integrate with other conveyor systems.
Gravity Roller Conveyors

Applications:
Warehouses for unloading and loading trucks.
Manufacturing facilities for transporting parts along assembly lines.
Cost-conscious operations looking for energy-free material movement.
Industries:
Warehousing
Manufacturing
Logistics
Mechanism: Uses a slight incline to create natural movement of items.
Cost & Maintenance: Low cost; minimal maintenance aside from occasional roller cleaning.
Key Features:
Energy-efficient, no power source required.
Simple design for easy maintenance.
Adjustable slopes for speed control.
Motorized Roller Conveyors

Applications:
Manufacturing plants with automated workflows.
Packaging industries for moving goods along production lines.
Distribution centers requiring flexible and energy-efficient solutions.
Industries:
Manufacturing
Packaging
Distribution
Mechanism: Each roller contains a motor that powers movement independently or in sync with others.
Cost & Maintenance: Higher cost; regular motor inspections and software updates.
Key Features:
Individual roller motors for flexible design.
Smooth, automated item movement.
Energy-efficient with zoned power usage.
PVC Roller Conveyors

Applications:
Packaging plants handling moisture-sensitive materials.
Warehousing environments exposed to chemical elements.
Cost-effective logistics operations needing lightweight rollers.
Industries:
Packaging
Warehousing
Logistics
Mechanism: Rollers made from PVC mounted on a standard frame.
Cost & Maintenance: Low cost; occasional roller replacement needed.
Key Features:
Lightweight yet durable.
Corrosion and moisture resistance.
Cost-effective material choice.
Poly-V Groove Roller Conveyors

Applications:
Manufacturing facilities moving pipes, tubes, and drums.
Distribution centers handling round or awkwardly shaped items.
Packaging plants requiring smooth transport of cylindrical products.
Industries:
Manufacturing
Distribution
Packaging
Mechanism: Uses grooved rollers to grip cylindrical objects securely.
Cost & Maintenance: Moderate cost; requires occasional groove inspection and cleaning.
Key Features:
Special groove profile for cylindrical stability.
Reduces item slippage.
Handles delicate items smoothly.
Power Roller Conveyors

Applications:
Warehouses and distribution hubs needing high-speed material movement.
Manufacturing lines demanding controlled item flow.
Logistics operations focused on precision handling.
Industries:
Warehousing
Distribution
Manufacturing
Logistics
Mechanism: Powered rollers connected to a central or distributed motor system.
Cost & Maintenance: Higher cost; regular motor checks and speed calibration.
Key Features:
Controlled item movement with adjustable speeds.
Handles heavy loads with ease.
Integrates well with automated systems.
Taper Roller Conveyors
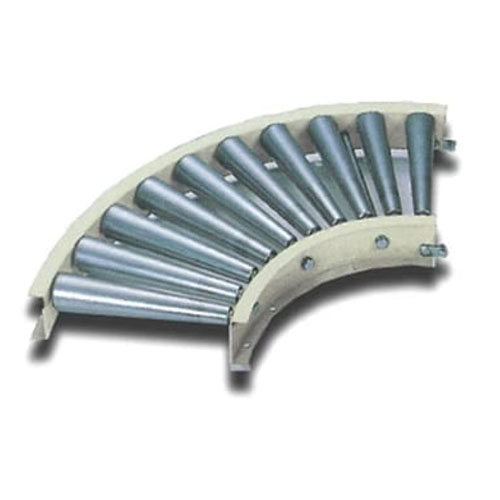
Applications:
Distribution centers consolidating different product lines.
Manufacturing processes requiring item accumulation.
Logistics setups aiming for smooth product merging.
Industries:
Distribution
Manufacturing
Logistics
Mechanism: Utilizes conical rollers to control the direction and speed of items merging into one line.
Cost & Maintenance: Moderate cost; needs regular roller alignment checks.
Key Features:
Accumulates products for streamlined merging.
Handles varying item sizes.
Ideal for multi-line merging processes.
Sortation and Accumulation Conveyors: Optimizing Material Flow

In the fast-paced world of material handling, sortation and accumulation conveyors are essential for keeping operations running smoothly. These advanced conveyor systems enhance productivity, streamline processes, and prevent costly disruptions. Let’s break down what they do and why they matter.
What Are Sortation Conveyors?
Sortation conveyors are designed to automatically identify, sort, and divert items or products to their appropriate lines or destinations. This process is based on various criteria, such as product type, size, or shipping information. These conveyors use technologies like:
Barcode scanning to read labels and direct products.
Weighing systems to sort items by weight.
Dimensioning tools to classify products by size.
By efficiently routing items, sortation conveyors improve accuracy and reduce manual handling, making them indispensable for industries like e-commerce, manufacturing, and distribution.
What Are Accumulation Conveyors?
Accumulation conveyors manage the flow and spacing of items on a conveyor line. When downstream processes slow down or pause, these conveyors allow products to accumulate without causing jams or damage. Once the line clears, the items are released and spaced out again.
Key features of accumulation conveyors include:
Zone-based control that starts and stops sections independently.
Specialized rollers or belts to control product movement.
Conical rollers to manage the direction and speed of items merging into one line.
This functionality prevents product collisions, reduces manual intervention, and maintains synchronized material flow.
Applications
Distribution centers consolidating different product lines.
Manufacturing processes requiring item accumulation.
Logistics setups aiming for smooth product merging.
Industries
Distribution
Manufacturing
Logistics
Cost & Maintenance
Cost: Moderate
Maintenance: Requires regular roller alignment checks
Benefits of Sortation and Accumulation Conveyors
Incorporating sortation and accumulation conveyors into your material handling system offers several advantages:
Increased Throughput and Productivity
These systems streamline material flow, minimize bottlenecks, and boost overall processing speed.
Improved Accuracy and Efficiency
Automated sorting ensures products reach their correct destinations with minimal errors.
Adaptability to Fluctuating Volumes
Accumulation conveyors handle variations in production or order volumes by temporarily storing items until the line clears.
Reduced Product Damage
By preventing jams and collisions, these conveyors protect items from unnecessary wear and tear.
Enhanced Worker Safety
Automation reduces the need for manual handling, lowering the risk of workplace injuries.
Operational Flexibility
These conveyors allow you to oversee multiple processes or stations simultaneously, keeping your facility agile and responsive.
Driving Efficiency Across Industries
Sortation and accumulation conveyors are vital for industries like:
E-commerce fulfillment centers handling high volumes of online orders.
Manufacturing plants ensuring smooth assembly line processes.
Distribution warehouses coordinating complex shipping and logistics operations.
By investing in these conveyor solutions, businesses can maintain high throughput rates, minimize downtime, and optimize material flow.
Overhead Conveyor Systems: Maximizing Space and Efficiency
Overhead conveyor systems provide an effective solution for material transport by utilizing overhead space, keeping floors clear and allowing seamless integration with other processes. These systems come in various types, each tailored to specific operational needs.
Types of Overhead Conveyor Systems
Hand Push Beam Trolley Systems:
Manually operated, with trolleys moved along an overhead track.
Best suited for light loads and short-distance material transport.
Motorized Overhead Conveyors (Monorails):
Powered by electric motors, moving carriers along a suspended track.
Ideal for automating material handling over longer distances.
Inverted Monorails and Inverted Power & Free Conveyors:
The track is positioned below the load, simplifying loading and unloading from multiple levels.
Commonly used in industries like automotive and aerospace for transporting large or bulky components.
Key Benefits
Space Optimization: Frees up valuable floor space for other operations.
Scalability: Easily integrates with existing processes, enhancing workflow.
Automation: Reduces manual handling, boosting productivity.
Safety Considerations
Regardless of the conveyor type, safety is a top priority. Proper measures must be implemented to protect workers from hazards such as falling objects and accidental collisions with moving parts. Routine maintenance and employee training are crucial to maintaining a safe working environment.
Overhead conveyors offer a smart, space-saving solution for industries requiring efficient material transport. From simple manual systems to complex automated solutions, these conveyors enhance productivity while ensuring workplace safety.
Specialized Conveyor Types

Screw Conveyor
Applications:
Transporting grains, seeds, and feed materials in agriculture.
Handling flour, sugar, and powders in food processing.
Conveying cement, sand, and minerals in mining and construction.
Moving powdered chemicals and raw materials in the chemical industry.
Industries:
Agriculture
Food Processing
Mining and Construction
Chemical
Mechanism: Utilizes a rotating helical screw blade (auger) to move materials along a cylindrical casing or trough.
Cost & Maintenance: Cost-effective solution; requires periodic inspection of the screw blade and casing for wear and tear.
Key Features:
Versatile design suitable for powders, granules, and semi-solids.
Customizable sizes and configurations.
Enclosed system to minimize spills and dust generation.
Provides controlled feeding and discharge of materials.
Aero-Mechanical Conveyor
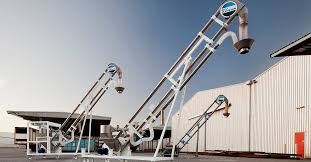
Applications:
Transporting dry, granular materials like powders and pellets.
Handling cement, sand, and other fine materials in construction.
Moving plastic granules and resin beads in plastics manufacturing.
Conveying powdered chemicals and additives in chemical processing.
Industries:
Cement
Plastics
Chemical
Food Processing
Mechanism: Uses a combination of air and mechanical forces to move materials through an enclosed tubular system, creating a fluid-like flow for smooth, high-speed transport.
Cost & Maintenance: Moderately expensive; requires regular checks on the rope, discs, and tubing for wear, along with monitoring airflow systems.
Key Features:
Enclosed design reduces dust and product loss.
Suitable for long-distance conveying.
Minimizes material degradation during transport.
High efficiency for moving lightweight, granular products.
Bucket Conveyor (Bucket Elevator)

Applications:
Lifting grains, seeds, and feed to higher levels in agriculture.
Elevating sand, gravel, and crushed stone in mining and construction.
Handling flour, sugar, and bulk food items in food processing.
Moving raw materials like cement and coal in industrial plants.
Industries:
Agriculture
Mining and Construction
Food Processing
Industrial Manufacturing
Mechanism: Features buckets attached to a rotating belt or chain, lifting materials vertically from a lower to a higher point.
Cost & Maintenance: Moderate to high cost; requires regular inspection of buckets, belts, and chains for damage and alignment.
Key Features:
Ideal for vertical material transport.
Handles bulk materials efficiently.
Available in continuous or centrifugal bucket designs.
Reduces spillage and material loss.
Pneumatic and Cable Conveyor Systems

Pneumatic Conveyor
Applications:
Transferring powders, pellets, and granules in food processing.
Conveying cement, fly ash, and fine particles in construction.
Moving plastic resins and granules in manufacturing.
Handling chemicals and pharmaceuticals in sanitary environments.
Industries:
Food Processing
Construction
Manufacturing
Chemical and Pharmaceutical
Mechanism: Uses air or gas to create differential pressure, pushing or pulling dry bulk materials through enclosed tubes or pipes. Operates in two modes:
Dilute-phase: High-velocity air keeps materials suspended, ideal for long distances.
Dense-phase: Low air velocity moves heavier concentrations of materials, suitable for shorter runs.
Cost & Maintenance: Moderate cost; minimal moving parts result in lower maintenance, but requires periodic checks of air pressure systems and pipe integrity.
Key Features:
Suitable for powders, granules, and free-flowing materials.
Flexible routing around obstacles.
Handles abrasive materials without conveyor damage.
Can be designed for hazardous or sanitary environments.
Cable Conveyor (Drag Conveyor)
Applications:
Transporting bulk materials like coal, sand, and gravel in mining and quarrying.
Moving raw materials in power plants.
Handling grains, seeds, and feed in agriculture.
Conveying large or abrasive materials in industrial processes.
Industries:
Mining and Quarrying
Power Plants
Agriculture
Industrial Manufacturing
Mechanism: Uses a continuous chain or cable to pull materials through an enclosed trough or casing, allowing for horizontal, inclined, or vertical transport.
Cost & Maintenance: Moderate to high cost; regular inspection of cables, chains, and casings is required to prevent wear and tear.
Key Features:
Effective for long-distance transport of bulk materials.
Can operate at various angles and elevations.
Suitable for handling large, heavy, or abrasive materials.
Enclosed design reduces spillage and dust.
Conveyor System Controls

Conveyor System Controls
Applications:
Regulating start, stop, speed, and direction of conveyors in manufacturing plants.
Coordinating multiple conveyor segments in automated production lines.
Integrating with sorting, tracking, and inspection systems in logistics and distribution.
Managing product flow in industries like food processing, mining, and packaging.
Industries:
Manufacturing
Logistics and Distribution
Food Processing
Mining and Construction
Mechanism: Conveyor controls range from basic electrical systems using motor controls to advanced automation solutions:
Basic Controls: Manage simple functions like starting, stopping, and adjusting conveyor speed.
Advanced Controls: Use Programmable Logic Controllers (PLCs) and industrial computers to coordinate conveyor segments, integrate with other machinery, and adjust operations in real time.
Cost & Maintenance: Varies with complexity; basic systems are cost-effective with minimal upkeep, while advanced systems require regular software updates, sensor calibration, and diagnostic checks.
Key Features:
Real-time monitoring and adjustments.
Integration with sorting, inspecting, and tracking systems.
Fault detection and diagnostic capabilities.
Remote access for maintenance and troubleshooting.
Compatible with Industry 4.0 technologies for smart automation.
Designing a Conveyor System
Designing a Conveyor System
Key Considerations:
Define Objectives: Clearly outline the system's purpose — whether for material transport, sorting, or production line integration.
Operational Analysis: Assess the working environment, including temperature, humidity, and space constraints.
Conveyor Selection: Choose the right type of conveyor (gravity, belt, screw, pneumatic, etc.) based on the materials being handled.
Layout Planning: Map the material flow, determine conveyor speeds, and calculate load capacities.
System Integration: Ensure smooth compatibility with existing equipment and automation controls.
Design Process:
Material Flow Mapping: Visualize how products will move through the system.
Speed and Load Calculations: Determine required conveyor speeds and maximum load capacities.
Layout Optimization: Adjust the design to fit facility space and accommodate potential obstacles.
Automation Integration: Plan for advanced controls, such as PLCs or sensors, for real-time monitoring and efficiency.
Expert Collaboration: Partnering with experienced systems integrators can streamline the design process. These specialists help:
Select the most suitable conveyor types.
Optimize layouts for maximum productivity.
Incorporate automation and control systems tailored to your operations.
Outcome: A well-designed conveyor system maximizes efficiency, reduces downtime, and seamlessly integrates into your facility, supporting smooth and reliable material handling.
Selecting the Right Conveyor
Key Considerations:
Product Specifications: Assess the size, weight, and material composition of the items to be conveyed.
Accumulation Needs: Determine if products need to pause or accumulate along the line without causing jams.
Washdown Requirements: Consider if the system needs to withstand frequent cleaning, especially in food processing or pharmaceutical environments.
Guide Rails: Evaluate whether guide rails are needed to keep products aligned during transport.
Environmental Assessment:
Space and Layout: Measure available space and plan how the conveyor will fit within the facility’s layout.
Integration: Ensure compatibility with existing machinery and automation systems.
Operating Conditions: Account for factors like temperature, humidity, and dust levels.
Expert Collaboration: Working with conveyor specialists can simplify the selection process. These experts assist in:
Recommending the most suitable conveyor type for your products and environment.
Designing custom solutions tailored to your operational needs.
Integrating emerging technologies for automation and energy efficiency.
Providing strategies to boost productivity and reduce downtime.
Kommentare