Understanding Pipe Stress Analysis: A Comprehensive Guide
- shiva ganesh
- Feb 27
- 5 min read
Updated: Apr 16

Pipe stress analysis is a critical aspect of piping design, ensuring the safety and reliability of piping systems used across various industries.
This guide provides a foundational understanding of pipe stress analysis, its objectives, applications, real-world examples, and practical insights.
Let’s dive into how stress impacts piping systems and why proper analysis is essential.
What is Pipe Stress Analysis?
Pipe stress analysis is an analytical method to determine how a piping system behaves under various conditions. It helps identify stresses due to thermal expansion, internal/external pressure, and other mechanical forces. The process considers factors such as:
Material properties: Carbon steel, alloy steel, stainless steel, FRP (Fiberglass Reinforced Plastic), GRP (Glass Reinforced Plastic), HDPE (High-Density Polyethylene).
Pressure: Design pressure, operating pressure, and hydro test pressure.
Temperature: Maximum design, maximum operating, and minimum design temperatures.
Fluid properties: Density, viscosity, and flow rates.
Support systems: Types and placements of supports, such as anchors, guides, and springs.
By inputting these parameters into specialized software like CAESAR II, AutoPIPE, and START-PROF, engineers can simulate the piping system’s behavior and assess thermal growth, displacements, and stress generation.
Real-world Example: In a refinery, high-temperature steam lines experience significant thermal expansion. Stress analysis ensures expansion joints and loops are correctly placed to prevent stress accumulation and equipment failure.
Application: In HVAC systems of commercial buildings, stress analysis ensures chilled water piping doesn’t crack under thermal contraction during cooling cycles.
Objectives of Pipe Stress Analysis
The primary objectives of pipe stress analysis are to ensure:
Structural Integrity: Ensuring the piping system can withstand internal and external pressures without failure. Stresses remain below code-allowable limits.
Operational Integrity: Ensuring the system operates without leaks or failures. Nozzle loads on connected equipment stay within allowable limits. Sagging and displacement are minimized.
Optimization: Designing cost-effective piping by avoiding excessive flexibility and managing loads on support structures.
Applications:

Power Plants: Analysis of steam piping systems to handle high-pressure, high-temperature conditions. For example, turbine inlet piping must be carefully analyzed for thermal expansion.
Chemical Plants: Managing thermal growth and vibration issues in process piping, such as analyzing reactor feed pipelines.
Offshore Platforms: Assessing wave and wind effects on risers and subsea pipelines, preventing fatigue failure.
Pharmaceutical Industry: Ensuring sanitary piping systems meet stringent regulatory requirements and withstand cleaning cycles.
Food Processing Plants: Designing piping systems for high-pressure steam sterilization processes.
Nuclear Plants: Stress analysis of reactor coolant systems to prevent thermal shock and ensure reactor safety.
Key Factors Triggering Stress

Several factors can trigger stress within a piping system:
Internal Factors:
Temperature: Variations cause expansion or contraction, leading to stress, especially if movement is restricted.
Pressure: Internal pressure exerts force on pipe walls, creating stress.
Velocity: Fluid velocity can cause impacts and vibrations, particularly at elbows.
Weight: The weight of the pipe, fluid, and insulation contributes to stress, especially if support is inadequate.
Example: In a chemical plant, rapid temperature changes during batch processing can cause thermal shock, necessitating careful stress analysis.
External Factors:
Wind Force: Wind can exert significant pressure, especially on tall structures.
Seismic Activity: Earthquakes introduce multi-dimensional forces that can destabilize piping systems.
Snowfall: Snow accumulation adds weight, potentially causing structural issues.
Wave Effects: Important for offshore structures, wave forces can impact piping systems.
Application: Offshore platforms require dynamic analysis to prevent riser damage due to wave-induced motion.
Understanding Stress and Strain
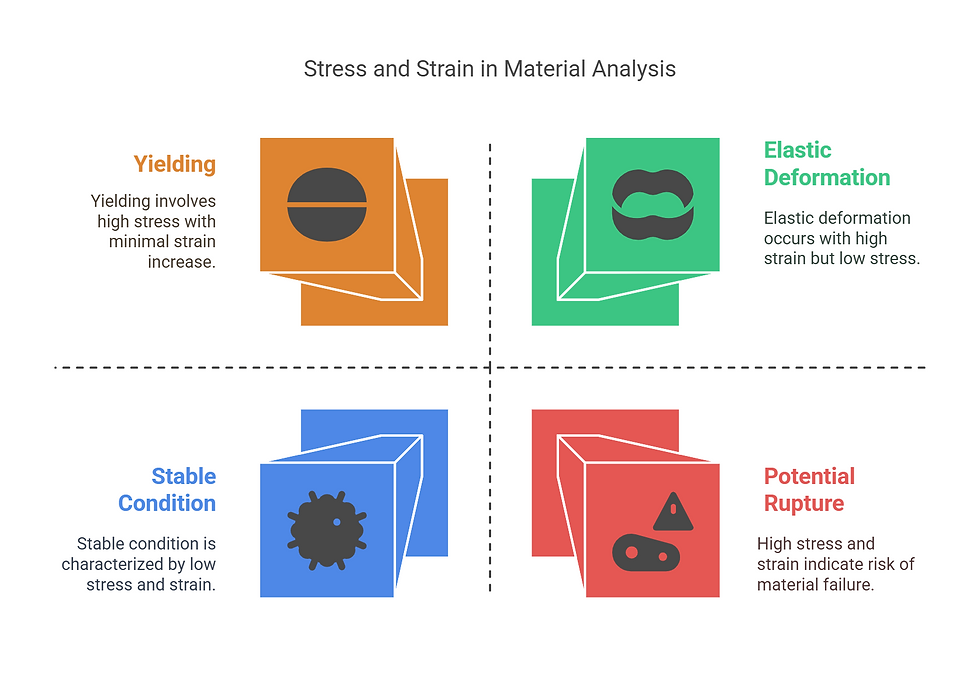
When discussing pipe stress analysis, it’s important to differentiate between stress and strain:
Stress: The force exerted on an object or material, typically measured in Pascals (Pa) or pounds per square inch (psi).
Strain: The deformation resulting from stress, calculated as the ratio of change in length to the original length.
Materials have a yield point, up to which deformation is reversible. Exceeding this point leads to plastic deformation and potential rupture.
Example: In a refinery, over-pressurization of a steam line may push carbon steel pipes beyond their yield point, risking rupture if stress isn’t properly managed.
Application: In natural gas pipelines, stress analysis prevents yielding at pressure peaks, ensuring long-term structural integrity.
ASME B31.3 and Allowable Stresses
ASME B31.3 is a crucial standard for process piping. It defines allowable stresses for various materials based on their tensile and yield strengths. For instance, A106 Grade B carbon steel has a tensile strength of 60 KSI and a yield strength of 35 KSI. Piping systems are designed to ensure forces remain within allowable limits, providing a safety margin.
Application: In a petrochemical plant, engineers use ASME B31.3 guidelines to design pipes that transport hazardous fluids, ensuring safety and compliance.
Example: Engineers designing ammonia pipelines in fertilizer plants rely on ASME B31.3 to control stress levels and prevent leaks.
Types of Stresses
Piping systems experience different types of stresses:
Sustained Stresses: Caused by constant loads like weight and pressure.
Expansion Stresses: Result from temperature changes and restricted thermal growth.
Occasional Stresses: Generated by short-term events like wind, earthquakes, or pressure surges.
Real-world Example: In a nuclear power plant, expansion stresses are carefully analyzed in reactor coolant systems to prevent thermal cracking.
Application: In heating systems, occasional stresses from rapid pressure surges during startup are mitigated through stress analysis.
Reducing Piping Stresses

To mitigate stress and maintain piping integrity, engineers can implement:
Proper Support: Adequate support is crucial for managing weight-related stresses.
Flexibility: Incorporating flexibility through expansion loops and directional changes can minimize thermal stresses.
Expansion Joints: While effective, expansion joints should be used cautiously due to cost and maintenance.
Guided Supports and Anchors: Controlling thermal growth by strategically placing fixed points and guided supports.
Snubbers and Dampers: Used to control dynamic forces, especially in seismic zones.
Example: In an LNG facility, expansion loops are added to cryogenic pipelines to absorb contraction during extreme cooling, ensuring structural integrity.
Application: Gas pipelines crossing bridges use guided supports to handle thermal expansion without overstressing joints.
Conclusion
Pipe stress analysis is a multifaceted field requiring a strong understanding of engineering principles, material properties, and industry codes and standards. By carefully considering all relevant factors and utilizing appropriate software tools, engineers can design safe, reliable, and efficient piping systems.
Whether you’re a professional engineer or someone looking to learn more about piping systems, understanding the fundamentals of pipe stress analysis is key to ensuring structural and operational integrity across industries.
Comments