What is Automotive BIW Product Design?
- Bhargava Krishna Marripati
- Feb 7, 2024
- 5 min read
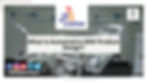
1. What is Automotive BIW Product Design?
Automotive Body-in-White (BIW) product design refers to the engineering and development of the structural components of a vehicle's body before painting and assembly. The BIW forms the skeleton onto which all the other components like doors, hoods, and bumpers are attached.
The BIW is made up of pressed panels that are welded together to create the floor plan, pillars, rails, and roof structure. It determines the overall shape, size, and structural rigidity of the vehicle body. The term "Body-in-White" comes from the color of the unpainted metal panels.
BIW design focuses on the load-bearing structure while body structure encompasses all body parts including closures like doors, hood, and trunk lid. BIW design and engineering is a crucial part of automotive development. It involves:
- Using advanced engineering software for BIW design, simulation, and validation
- Material selection and lightweight of body components
- Stamping and forming processes for panel preparation
- Structural performance under crash, NVH, and durability conditions
- Welding and joining techniques for panels
- Optimization of modularity and parts consolidation
Getting the BIW design right is critical for vehicle safety, quality, manufacturing efficiency, and meeting weight targets. The increasing focus on fuel economy and lightweight materials is also driving innovation in BIW engineering. With new trends like electric vehicles, autonomous driving, and connectivity, BIW design continues to evolve to meet future mobility needs.
2. BIW Design Requirements
The automotive body-in-white (BIW) forms the skeleton of a vehicle and as such, has to meet stringent design requirements. Here are some of the key considerations for BIW design:
Safety Regulations
The BIW design needs to comply with various safety regulations that are mandated in the target markets for the vehicle. Some key safety requirements include:
- Crashworthiness - the ability of the BIW structure to protect occupants in crashes
- Impact standards - meeting regulations like the European New Car Assessment Program and US Federal Motor Vehicle Safety Standards for frontal, side and rear crashes
- Passenger safety cell - providing adequate survival space for passengers in case of rollover
Performance Requirements
In addition to safety, the BIW needs to fulfill several performance requirements:
- Durability - the ability to withstand vibrations and forces during the vehicle's lifetime without failure
- Noise, vibration, and harshness (NVH) - minimizing noise and vibrations for ride comfort
- Torsional rigidity - providing stiffness to resist twisting forces
- Dent resistance - the ability to resist minor dents and maintain structural integrity
Manufacturing Constraints
The BIW design must enable efficient and feasible manufacturing through techniques like:
- Stamping - match designs to the limits of stamping presses
- Welding - incorporate weldable joints and minimize welding operations
- Dimensional accuracy - account for manufacturing tolerances
- Part reduction - minimize part count for simplified assembly
Cost Targets
A key requirement is meeting cost targets which requires:
- Design for manufacturing - enable ease of production with less waste
- Lightweighting - use high-strength materials to reduce weight
- Part integration - design integrated parts instead of assemblies
- Standardization - leverage common parts across models
The BIW design has to strike an optimal balance between all these considerations. Safety and performance are non-negotiable while production feasibility and costs need to be optimized.
3. Key Steps in the BIW Design Process
The key steps in designing an automotive BIW include:
Conceptual Design
The first step is developing the conceptual design. This involves creating initial sketches and 3D models to visualize the basic vehicle package and body structure. Key decisions are made about the overall vehicle size, shape, seating layout, door configurations, and more. Aerodynamics, styling, ergonomics, and practical considerations all play a role at this stage.
Computer Aided Engineering
Once the basic conceptual design is established, engineers use computer-aided engineering (CAE) software to start modeling and analyzing the BIW structure in detail. Advanced FEA, CFD, and other simulations help evaluate and optimize factors like torsional rigidity, crashworthiness, NVH, weight reduction, manufacturability, and costs. Different materials and manufacturing methods are modeled digitally.
Prototyping and Testing
Prototypes of the BIW structure are built and subjected to various tests to validate the design. These include structural, safety, NVH, and fatigue tests. Data from physical testing allows engineers to refine the CAE models and simulations. Multiple design-build-test loops are conducted to optimize the BIW design. Test results are compared to regulatory and performance requirements.
Design Validation
The final step is design validation where the complete BIW design is verified to meet all engineering, manufacturing, and regulatory requirements. Safety rating tests are conducted on prototypes to ensure crashworthiness. Manufacturing trials are done to validate producibility and quality standards. The BIW design receives final approval before full production begins.
4. BIW Materials
The selection of materials is critical in BIW design as it impacts the vehicle's weight, safety, performance, and cost. Here are some key points on materials used in BIW:
Steel continues to be the primary material for BIW due to its strength, formability, and low cost. Common steel grades used are:
- High strength low alloy (HSLA) steels - Offer high strength with good formability and weldability. Widely used for pillars, rails, cross members, etc.
- Advanced high-strength steels (AHSS) - Provide ultra-high strength while maintaining ductility. Used in small amounts for reinforcing pillars, sills, bumper, etc.
- Bake hardenable (BH) steels - Offer improved strength after the paint baking process. Used for body panels.
- Dual-phase (DP) steels - Excellent combination of high strength and ductility. Used for body structure parts.
- Martensitic steels - Very high strength but less formable. Used where high strength is critical.
Aluminum is gaining popularity for its lightness, corrosion resistance, and recyclability. Aluminum parts are joined using rivets, adhesives, or welding. The latest trend is using aluminum alloy castings for complex parts.
Other lightweight materials like magnesium alloys, carbon fiber-reinforced plastics, and high-strength plastics are also being adopted, especially in electric vehicles, to further reduce weight.
Multi-material design, combining steel, aluminum, and plastics is an emerging trend to optimize weight, performance, and cost. Advanced joining methods like laser welding facilitate the mixing of materials.
5. BIW Manufacturing Processes
The manufacturing of the automotive body-in-white primarily relies on metal-forming technologies like stamping, hydroforming, laser welding, and structural adhesives.
Stamping
Stamping is the most common BIW manufacturing process. It involves the use of dies to transform sheet metal into complex 3D shapes with high precision. The press stamping operations include blanking, bending, drawing, flagging, and piercing. Computers help optimize the die design and simulate the forming process. Materials like high-strength steel, aluminum, and advanced alloys are formed using stamping.
Hydroforming
Hydroforming uses pressurized fluid to form tubular or sheet metal blanks into complex shapes. It allows parts to be made with concave, convex, and other complex geometries. Tubes are placed inside die cavities and high-pressure hydraulic fluid is pumped in to expand and form the material. Hydroformed parts have increased stiffness and reduced weight co...
Output trimmed for rendering. Click copy for full output.
1. Building the Backbone: A Deep Dive into Automotive BIW Design
2. The Secret Source Code Behind Your Car's Body: Decoding Automotive BIW
3. What's Under the Hood? Demystifying Automotive BIW Product Design
Explore automotive BIW design, its impact on vehicles, assembly, lightweight trends, and future outlooks.