What is Reverse Engineering in Mechanical CAD? Exploring Techniques and Applications
- Bhargava Krishna Marripati
- Feb 19, 2024
- 11 min read
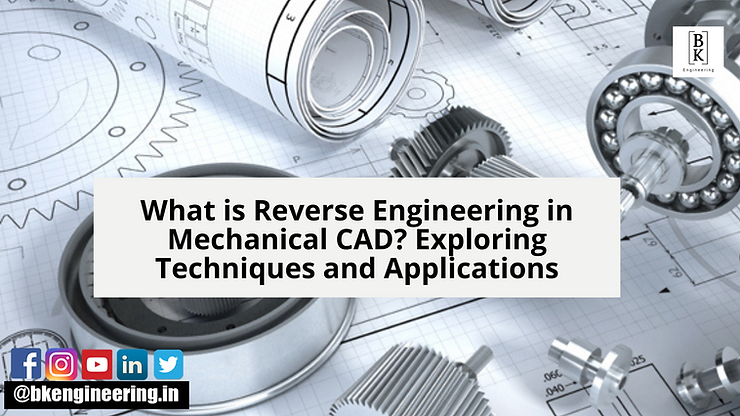
What is Reverse Engineering in Mechanical CAD?
Reverse engineering in mechanical CAD refers to the process of obtaining a 3D CAD model from an existing physical part. It involves capturing the geometric design data from the part and then using this to recreate a 3D CAD model.
The goal of reverse engineering is to analyze the design, engineering, and functionality of an existing part to understand how it was made and how it works. This CAD model can then be used to manufacture identical or improved versions of the original part.
Reverse engineering has several important applications in mechanical engineering and product design:
Recreating legacy parts that are no longer in production
Creating spare parts for maintenance and repairs
Understanding the design and engineering of competitors' products
Improving an existing product by analyzing its weaknesses
Creating compatible components that integrate with existing products
Innovating new products by understanding what's already been done
The key benefits of reverse engineering in mechanical CAD include:
Saving time and money compared to designing a part from scratch
Maintaining access to out-of-production parts
Uncovering hidden innovations in existing products
Bridging compatibility gaps between new and legacy systems
Reducing development risk by building on proven designs
By scanning an object to capture its exact geometry and then modeling this in CAD software, reverse engineering provides crucial design information that can accelerate the product development cycle. It is a valuable tool for mechanical engineers across many industries and applications.
Why Reverse Engineer Parts and Products?
Reverse engineering provides numerous benefits for companies looking to analyze competitor products, reproduce legacy parts, reduce costs, and improve designs. Here are some of the key reasons companies invest in reverse engineering:
Understand Competitors - Reverse engineering allows companies to deeply understand the designs, components, and manufacturing processes used by competitors. This competitive intelligence enables strategic planning and motivates product improvements.
Recreate Legacy Parts - For companies that rely on outdated components that are no longer in production, reverse engineering is the only option to reproduce replacement parts. Aerospace and defense companies often reverse engineer obsolete parts to keep fleets operational.
Improve Designs - By benchmarking competitor products, companies can uncover design optimizations and innovations worth integrating into their own products. Reverse engineering fuels incremental and disruptive innovation.
Reduce Costs - Analyzing a competitor's design and manufacturing methods can reveal more efficient approaches. This allows companies to reduce material costs, streamline manufacturing, and optimize their supply chains.
Meet Interoperability Needs - In technology, reverse engineering helps create compatible products and ensure interoperability between devices. For example, third party printer manufacturers reverse engineer protocols to support proprietary printers.
Shorten Development Cycles - The insights gained from reverse engineering competitor and legacy products significantly reduce development and testing timelines for new product introduction.
Reverse engineering provides strategic value for organizations across industries. It enables both offensive and defensive innovation, positioning companies to compete at the leading edge of their markets.
Reverse Engineering Process Steps
Reverse engineering a mechanical part involves a multi-step process to go from the physical part to a 3D CAD model that can be used for manufacturing. Here are the key steps in the reverse engineering workflow:
3D Scanning
The first step is to capture geometric data from the physical part using a 3D scanner. The scanner uses laser, structured light, or other technologies to capture thousands of data points on the part's surface to create a 3D point cloud. Popular scanners for mechanical reverse engineering include structured light scanners like the EinScan Pro 2X and industrial CT scanners from Nikon Metrology. The scanner produces an initial 3D scan data file such as an STL.
Point Cloud Processing
The raw scan data must be cleaned up and optimized to create a refined point cloud suitable for CAD modeling. This involves mesh editing to fill holes, remove noise, optimize topology, and reduce file size while retaining accuracy. Point cloud processing software like Geomagic for SOLIDWORKS, Rapidform XOR, or MeshLab can edit STL and point cloud files for reverse engineering. The final point cloud represents an accurate digital replica of the part.
3D Modeling
Next, CAD modeling software converts the optimized point cloud into a high quality 3D model suitable for engineering and manufacturing. Popular mechanical CAD packages like SOLIDWORKS, Siemens NX, and Autodesk Inventor have specific reverse engineering workflows to convert scan data into feature-based CAD geometry. The final model is an accurate 3D representation of the original part in CAD software.
Prototyping
3D printing can create physical prototypes of the CAD model for testing form, fit, and function. SLA, SLS, and FDM 3D printing are commonly used to print prototype parts from the reverse engineered 3D model before final manufacturing. Prototyping validates the accuracy of the CAD model compared to the original part.
Production
Once the CAD model is refined and validated, it can be used for production manufacturing through CNC machining, injection molding, or other methods suitable for the material and part geometry. The validated CAD model serves as the digital master for manufacturing either replacement legacy parts or improved designs.
Reverse engineering successfully converts a physical part into a digital CAD model suitable for recreating or improving the original design. It requires specialized 3D scanning equipment, software, and an understanding of the involved workflows. When done effectively, reverse engineering allows legacy or outdated parts to be reproduced, replicated, or enhanced using contemporary manufacturing methods.
3D Scanning for Reverse Engineering
3D scanning is a crucial step in the reverse engineering workflow that allows capturing the physical geometry of an object digitally. This data is then used as the starting point for creating a 3D CAD model. There are several methods and technologies for 3D scanning:
Laser Scanning
Uses a laser beam to capture millions of points on the object's surface
Creates a dense point cloud with detailed color and geometry data
Ideal for large objects like buildings and landscapes
Long range scanners can scan from over 100 meters away
Structured Light Scanning
Projects a pattern of light onto the object and uses cameras to capture distortions
Can achieve accuracy down to 50 microns
Well suited for medium sized objects
Limited working range of 0.3 - 5 meters
Photogrammetry
Creates 3D models from overlapping 2D photographs taken at multiple angles
Requires minimal equipment - just a camera and software
Lower resolution than laser scanning which limits engineering applications
There are many types of 3D scanners optimized for particular applications:
Handheld scanners for small objects
Arm CMM scanners for precision metrology
Industrial in-line scanners for manufacturing QA
Portable tripod scanners for field work
The key specifications for 3D scanners are resolution, accuracy, and scan volume. Resolution determines the detail visible on the 3D model. Accuracy measures how closely the model matches the real object's dimensions. Scan volume is the maximum size of object that can be captured.
Reverse engineering requires high accuracy - typically within 0.1-0.2mm - and resolution to capture fine design details. Scanners with blue or white structured light are well suited for this. Photogrammetry lacks the precision needed for engineering design work.
Point Cloud Processing
Once a physical object has been 3D scanned, the next step is processing the raw scan data, known as the point cloud. The point cloud represents millions of geometric samples on the surface of the object. Point cloud processing involves importing the scan data into software, cleaning it up, and optimizing it in preparation for CAD modeling.
Some key aspects of point cloud processing include:
Importing - The raw scan data must first be imported into specialized software like Geo magic for point cloud processing. Most scanners output data in common formats like OBJ, PLY, STL or their own native format. The software should support importing all major formats.
Cleaning - Raw scan data contains noise, outliers, holes, and other artifacts that must be cleaned up. This involves using tools like noise reduction filters, outlier deletion, and hole filling. Cleaning improves mesh quality for better CAD conversion.
Registration - For large objects, multiple scans are taken from different angles. Each scan has its own coordinate system that must be aligned through a process called registration. This combines the separate scans into a unified point cloud.
Optimization - Point cloud density is reduced while preserving all vital shape details. This optimization makes the point cloud lighter and easier to handle for later CAD modeling. Decimation tools quickly optimize heavy datasets.
Validation - The optimized point cloud is validated against the original scan for accuracy. Measurements of key dimensions are verified before the CAD conversion process begins. This ensures the CAD model will precisely match the actual physical object.
Proper point cloud processing turns raw scanned data into a clean digital representation of the real-world part geometry ready for CAD modeling. Mastering these point cloud steps leads to higher quality reverse engineered CAD models.
Converting Scan Data to CAD Models
The core of the reverse engineering process is taking the 3D scan data and converting it into a high quality 3D CAD model that can be used for prototyping and production. There are several challenges inherent in turning large, unstructured point clouds into clean parametric CAD models.
Point Cloud Preprocessing
Before converting the scan data into CAD, the point cloud must be optimized and cleansed of noise, outliers, holes, and irregularities that resulted from the 3D scanning process. This preprocessing ensures the point cloud is smooth, consistent, and ready for CAD modeling.
Surface Modeling
For organic and freeform shapes, surface modeling is an effective technique for converting scan data to CAD. The point cloud is used to fit and build complex surfaces that smoothly interpolate the scanned points. Common tools for surface modeling include surfacing in SolidWorks, Rhino, and Meshmixer.
Parametric vs Direct Modeling
Parametric CAD packages like SolidWorks allow the reverse engineered parts to be modeled with dimensions, constraints, and design intent. This helps modify designs down the line. Direct modeling packages like Autodesk Fusion 360 focus on fast direct geometry editing rather than history-based parametric modeling.
CAD Software Choices
Common CAD packages used include SolidWorks, Siemens NX, PTC Creo, Autodesk Inventor, CATIA, and Autodesk Fusion 360. The choice depends on surface quality needs, the capabilities of the software, and the downstream use of the CAD model.
The key is choosing the right CAD modeling strategy to accurately convert the scan data into a usable CAD model while maintaining the overall shape, form, fit, and function of the original part.
Rapid Prototyping in Reverse Engineering
Once a 3D CAD model has been created from the scan data, engineers will often 3D print prototypes of the part. This allows them to evaluate the accuracy of the CAD model by comparing the physical prototype to the original part.
Rapid prototyping is a key step in the reverse engineering workflow as it enables validation and refinement of the CAD model. Engineers can print multiple iterations, making tweaks to the CAD model between prints until an acceptable accuracy is achieved.
Some of the benefits of incorporating rapid prototyping into the reverse engineering process include:
Validating overall shape, geometry, and measurements
Testing form, fit and assembly of interfacing parts
Evaluating aesthetic appearance like textures and finishes
Performing functionality tests on working prototypes
Identifying improvements or design changes for the product
With recent advances in 3D printing technology, prototypes can now be printed quickly and cost-effectively even for complex geometries. The use of desktop 3D printers allows engineers to print new iterations and refine prototypes rapidly within their office.
Common 3D printing technologies used for rapid prototyping include FDM (fused deposition modeling), SLA (stereolithography) and SLS (selective laser sintering). Materials range from plastics like ABS and PLA to metals, allowing functional prototypes to be created.
Overall, the integration of rapid prototyping methods like 3D printing into reverse engineering enables improved recreation of legacy parts and accelerated product development. Validating CAD models prior to manufacturing reduces errors and speeds time-to-market for reverse engineered products.
Manufacturing from Reverse Engineered CAD
Reverse engineering produces a complete CAD model that can be used to manufacture the part or product through various methods. Common manufacturing processes utilized with reverse engineered CAD data include:
CNC Machining
CNC machining takes a CAD model and uses it to program the motion of a CNC machine to replicate the part. CNC machines use subtractive manufacturing, cutting away material with high precision tools to achieve the desired geometry. CNC machining is ideal for low volume production or custom parts. The CAD model provides the exact toolpaths needed to machine the part.
Injection Molding
For mass production, the CAD model can be used to design and manufacture injection molds. Injection molds are then used to produce plastic parts efficiently through injection molding. The CAD model provides the detailed contour data to craft injection molds that can produce parts identical to the original.
Casting
Metal casting is another manufacturing process compatible with reverse engineered CAD. The CAD model is used to create patterns and molds for sand casting or die casting of metal components. This allows fast, consistent reproduction of complex casted parts.
Tooling Design
In some cases, new tooling may need to be designed to produce the reverse engineered part. The CAD model provides the comprehensive specifications to engineer and prototype the required tools, jigs, or fixtures needed for manufacturing.
Reverse engineering enables reproducing parts through the manufacturing method best suited to requirements like part quantity, materials, and precision. The power of reverse engineering is unleashed when combining scanned data with advanced CAD modeling and manufacturing technologies.
Legal and Ethical Considerations
Reverse engineering often comes with important legal and ethical implications that engineers must consider.
Intellectual Property Laws
If done for commercial purposes without permission, reverse engineering a product may infringe on the intellectual property rights of the original manufacturer. Patents, trademarks, copyrights, and trade secrets may all be violated if reverse engineering results in reproducing a product for profit without authorization. However, reverse engineering for research, education, or to understand interoperability may be permissible under fair use exemptions to IP laws.
Fair Use Exemptions
In many countries, reverse engineering for research, teaching, or interoperability purposes is permitted under fair use provisions in intellectual property laws. This allows engineers to study products to advance learning or ensure compatibility between new and existing products. But fair use rules usually prohibit commercially exploiting reverse engineered products.
Corporate Espionage
Reverse engineering a competitor's product simply to steal trade secrets or destroy their advantage is unethical and in many cases illegal. Corporate espionage undermines ethical competition and innovation. However, benchmarking competitors via reverse engineering may be appropriate to understand the current state of the art and spur new advancements. The line between unethical and ethical reverse engineering isn't always clear.
Responsible Reverse Engineering
Engineers should ensure reverse engineering is done legally and ethically by considering fair use rules, respecting IP rights, and avoiding corporate espionage. The purpose and application of the reverse engineered information determines if the practice is permissible or not. Responsible reverse engineering upholds both the law and ethical standards.
The Future of Reverse Engineering
Reverse engineering techniques and technologies continue to rapidly advance, opening up new possibilities across many industries. Here are some of the key trends and innovations shaping the future of reverse engineering:
Emerging Scanning Technologies
Higher precision and speed - New structured light and laser scanning systems can capture highly detailed scans in a fraction of the time. Handheld scanners are also improving in terms of portability and accuracy.
Scanning smaller and internal features - Computed tomography (CT) scanning can capture the internal geometry of parts by taking X-ray images from different angles. This enables reverse engineering of complex assemblies and components.
Better material recognition - Spectral analysis techniques can help determine material composition during the scanning process. This provides useful information for downstream remanufacturing.
Enhanced Point Cloud Processing
Smarter AI algorithms - Machine learning is being applied to automate point cloud processing tasks like noise reduction, feature recognition, and conversion to CAD models. This reduces manual processing time.
Tighter CAD integrations - New tools allow CAD packages like SolidWorks to directly ingest scan data, making the modeling process more efficient.
Applications in Emerging Fields
Biomedical - Reverse engineering is enabling customized implants, prosthetics and artificial organs based on patient scans.
Heritage preservation - Scanning and modeling of historical artifacts and sites provides digital preservation and facilitates restoration.
Forensics - Crime scenes and evidence can be digitally preserved through 3D scanning and modeling.
As costs continue falling and technology improves, reverse engineering will become a standard part of the product design, manufacturing and maintenance lifecycle across nearly every industry. The future looks bright for this emerging field!