What is Sheet Metal Design in CAD? Exploring Techniques for Mechanical Components
- Bhargava Krishna Marripati
- Feb 19, 2024
- 3 min read
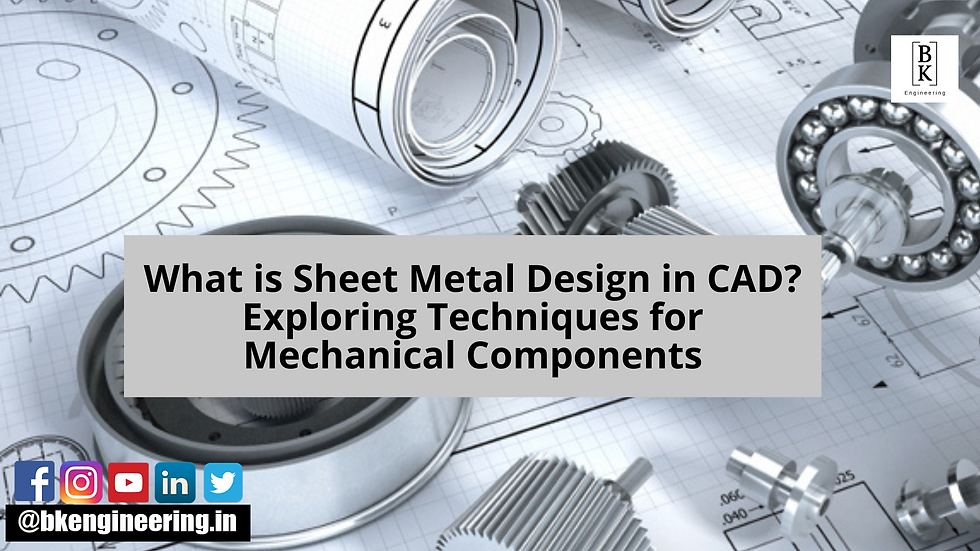
What is Sheet Metal Design in CAD? Exploring Techniques for Mechanical Components
Sheet metal design is a specialized discipline within Computer-Aided Design (CAD) that focuses on creating mechanical components from thin, flat sheets of metal. From simple enclosures to intricate assemblies, sheet metal parts are ubiquitous in industries such as automotive, aerospace, and electronics. In this blog post, we'll delve into the fundamentals of sheet metal design, exploring key techniques, considerations, and best practices for designing mechanical components using CAD software.
Understanding Sheet Metal Design
Sheet metal design involves the creation of parts and assemblies made from thin, flat sheets of metal, typically ranging in thickness from a few millimeters to a few centimeters. Unlike traditional solid modeling techniques, which focus on creating volumetric shapes, sheet metal design emphasizes the manipulation of 2D profiles and bends to achieve desired geometries.
Key Techniques in Sheet Metal Design
Bend Allowance and Bend Deduction:
Bend allowance and bend deduction are critical factors in sheet metal design, determining the amount of material deformation and stretch that occurs during bending operations. Understanding these concepts helps designers accurately predict the final dimensions and tolerances of sheet metal parts.
Flanges and Tabs:
Flanges and tabs are features commonly used in sheet metal design to provide strength, rigidity, and attachment points for fasteners or other components. Flanges extend perpendicular to the main body of the part, while tabs are smaller protrusions used for alignment or connection purposes.
Corner Relief:
Corner relief is a design feature that prevents material distortion and tearing during bending operations, particularly in tight corners or acute angles. By adding relief cuts or fillets to internal corners, designers can ensure smooth, consistent bends without compromising part integrity.
Forming Tools:
Forming tools are predefined shapes or features used to create complex geometries in sheet metal parts. Examples include embosses, lances, ribs, and louvers, which can be applied to sheet metal profiles to add functionality or aesthetic appeal.
Considerations for Sheet Metal Design
Material Selection:
Choosing the right material is crucial in sheet metal design, as different metals have unique properties and behaviors during forming and fabrication processes. Factors to consider include strength, ductility, corrosion resistance, and cost.
Manufacturability:
Design for manufacturability (DFM) principles are essential in sheet metal design to ensure that parts can be produced efficiently and cost-effectively. Minimizing complexity, reducing tooling requirements, and optimizing nesting layouts are key considerations for DFM.
Tolerance and Fit:
Sheet metal parts often require tight tolerances and precise fits to ensure proper assembly and functionality. Designers must carefully consider dimensional variations, material thickness, and manufacturing processes to achieve desired tolerances and fits.
Best Practices for Sheet Metal Design
Start with a Flat Pattern: Begin the design process by creating a flat pattern representation of the part, including bend allowances and relief features.
Use Symmetry: Exploit symmetry wherever possible to reduce design complexity and minimize material waste.
Consider Manufacturing Constraints: Consult with manufacturing engineers early in the design process to identify potential manufacturing constraints and optimize designs accordingly.
Iterate and Test: Iterate on designs and perform virtual simulations or physical prototypes to validate manufacturability, fit, and performance.
Conclusion
Sheet metal design is a specialized discipline within CAD that offers unique challenges and opportunities for mechanical designers. By understanding the key techniques, considerations, and best practices outlined in this blog post, designers can create robust, efficient, and manufacturable sheet metal components that meet the demands of modern engineering applications.
Comments